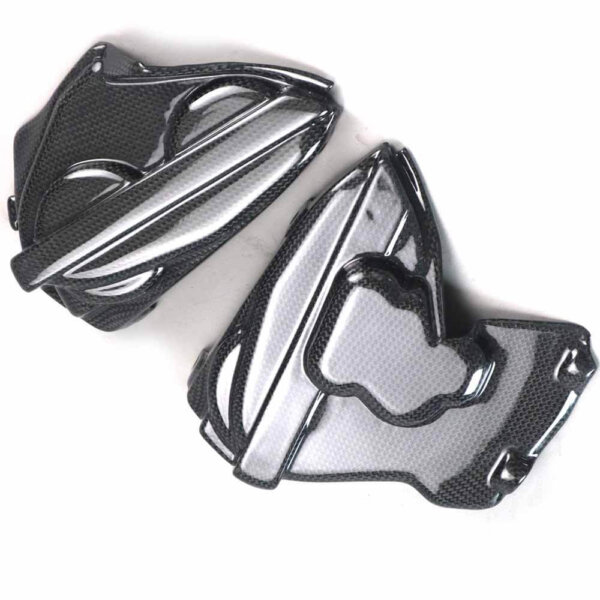
Si i bëjmë pjesët e fibrave të karbonit: Nga fillimi në fund
Problemi i madh me fibrat e karbonit
Prodhimi i pjesëve me fibra karboni është e vështirë. Shumë kompani përpiqen t'i bëjnë ato, por ngatërrohen. Pse? Ata nuk i dinë hapat e duhur. Ata përdorin materiale të këqija. Ata nxitojnë punën. Kjo çon në pjesë të dobëta atë pushim. Ajo çon në pjesë që nuk përshtaten siç duhet. Ajo çon në pjesë që duken keq.
Keni nevojë për pjesë të forta që nuk thyhen? Keni nevojë për pjesë që përshtaten siç duhet? Keni nevojë për pjesë që duken mirë?
Këto probleme i bëjnë blerësit të zemëruar. Ata shpërdorojnë para. Ata humbasin kohë. Ata duhet të fillojnë nga e para.
Pse kjo bëhet më keq
Problemi përkeqësohet kur:
- Ju duhet shumë pjesë të shpejta
- Ju duhen pjesë që përputhen siç duhet
- Keni nevojë për ndihmë për rregullimin e dizajnit
- Duhet të respektoni rregulla strikte
- Ju duhet çmimi më i mirë për pëlhurën me fibër karboni.
Kur gjërat shkojnë keq me pjesët me fibër karboni, mund të ndalojë të gjithë projektin tuaj. Makinat ulen përgjysmë. Biçikletat nuk mund të shiten. Avionët ngecin në tokë.
Blerësit ndihen të bllokuar. Ata kanë shpenzuar para, por nuk kanë pjesë të mira. Ata humbasin datat e nisjes. Klientët e tyre tërbohen.
Përgjigja jonë e thjeshtë: 28+ vite për ta bërë atë të drejtë
Ne e dimë se si t'i bëjmë pjesët me fibra karboni në mënyrën e duhur. E kemi bërë për 28+ vjet. Ne përdorim materialet më të mira. Ne ndjekim hapat e duhur. Ne kontrollojmë punën tonë pa pushim.
Le t'ju tregojmë se si e kthejmë fibrën e karbonit në pjesë që do t'ju pëlqejnë.
Hapi 1: Ne zgjedhim materialet e duhura
Ne fillojmë me materialet më të mira:
Lloji i materialit | Çfarë bën | Pse ka rëndësi |
---|---|---|
pararendës PAN | Blloku kryesor i ndërtimit të fibrave | I bën pjesët të forta |
Fibra me bazë linjine | Një opsion i gjelbër që kushton më pak përdor fibër karboni me epoksi. | Përdor 40% më pak para për të fituar |
Përgatitja e materialeve | Fibra karboni me rrëshirë tashmë në të rrit forcën e përbërë. | I bën pjesët më të njëjta |
Fibër karboni të ricikluar | Fibra e ripërdorur për disa pjesë | Ndihmon tokën, kushton më pak |
Ne zgjedhim atë që funksionon për punën tuaj. Keni nevojë për pjesë që janë super të forta? Ne përdorim fibër karboni të shkallës së hapësirës ajrore. Duhet të kurseni para? Mund të përdorim disa fibra karboni të ricikluara që ende funksionojnë mirë.
Hapi 2: Ne i japim formë fibrës siç duhet
Tani e kthejmë fibrën në formën që ju nevojitet. Ne përdorim këto mënyra:
- Infuzion me vakum – Për pjesë të mëdha e të lehta
- Prepreg derdhur – Për pjesë super të forta
- printim 3D – Për forma të shpejta dhe të ndërlikuara
- Derdhja e transferimit të rrëshirës – Për pjesë të lëmuara
- Teknologjia LFI – Për të bërë shpejt shumë pjesë
Çdo mënyrë ka pika të mira. Pjesët tona të makinave me fibër karboni duhet të jetë super i fortë. Pra, ne shpesh përdorim formimin e prepreg për ta.
Për pjesë me fibër karboni me porosi, ne mund të përdorim printimin 3D. Na lejon të bëjmë forma të çuditshme shpejt.
Hapi 3: Ne i bëjmë pjesët të forta
Më pas, ne i bëjmë pjesët të forta. Ne e përdorim ngrohjen në një mënyrë të zgjuar.
Mënyrat e vjetra përdorin shumë fuqi. Mënyrat tona të reja përdorin më pak:
- Ngrohje me mikrovalë – Përdor 70% më pak energji
- Teknologjia e plazmës – I bën pjesët po aq të forta, por më të shpejta
- Kurim i zgjuar – Përdor nxehtësinë e duhur në kohën e duhur
Kjo kursen para. I bën pjesët gati më shpejt me një teknikë të saktë të shtrimit. Ai gjithashtu ndihmon tokën duke përdorur procese të qëndrueshme prodhimi.
Hapi 4: Sigurohemi që pjesët janë perfekte
Ne kontrollojmë secilën pjesë në shumë mënyra:
- Ne e shikojmë nga afër
- Ne e masim atë
- Ne testojmë se sa i fortë është
- Ne shohim nëse përshtatet siç duhet
- Sigurohemi që të duket bukur
Nëse një pjesë nuk është e drejtë, ne nuk e dërgojmë atë. Kjo do të thotë që ju merrni vetëm pjesë të mira.
Si ju ndihmon rruga jonë të fitoni
Mënyra jonë për të bërë pjesë me fibër karboni ju ndihmon në mënyra të mëdha:
Për prodhuesit e makinave
Ne bëjmë pjesë që:
- Janë të lehta por të forta
- Dukeni shkëlqyeshëm
- Përshtatet siç duhet
- Kaloni të gjitha testet e sigurisë
Tona pjesë makinash me fibra karboni ndihmoni makinat të ecin më shpejt duke përdorur më pak gaz.
Për Ndërtuesit e Biçikletave
Ne bëjmë pjesë që:
- Janë super të lehta
- Dukeni të lezetshme
- Janë të fortë në përplasje
- Zgjat një kohë të gjatë
Shikoni tonë pjesë të motoçikletës me fibër karboni që kalorësit e duan.
Për prodhuesit e avionëve
Ne bëjmë pjesë që:
- Respektoni rregullat strikte të ajrit
- Janë të njëjta çdo herë
- Kurseni shumë peshë
- Qëndroni ndaj përdorimit të ashpër
Tregime të vërteta suksesi
Historia 1: Konsola e re e BMW-së
BMW kishte nevojë për një pjesë qendrore për një makinë të re që do të vinte në 2027. Ata e donin atë të lehtë. E donin të fortë. Ata donin që ajo të dukej mirë.
Ne përdorëm mënyrën tonë të printimit 3D për ta bërë atë me pëlhurë me fibër karboni. Kjo shkurtoi kohën me 40%. Gjithashtu kurseu peshë. BMW e pëlqeu atë.
Historia 2: Pjesët e energjisë së erës
Një kompani e energjisë së erës kishte nevojë për pjesë të mëdha që nuk prisheshin. Ata kishin nevojë që ato të zgjasin 20+ vjet jashtë. Dhe ata kishin nevojë për një çmim të mirë.
Ne përdorëm metodën tonë CARBOWAVE. Ai shkurtoi përdorimin e energjisë me 70%. I bënte pjesët po aq të forta. Kompania kurseu para dhe mori pjesë të shkëlqyera.
Historia 3: Ekipi i makinave të garave
Një ekip garash kishte nevojë për pjesë të reja shpejt. Të vjetrat e tyre u thyen. Gara u zhvillua për dy javë.
Ne bëmë pjesë të reja, më të mira në vetëm 10 ditë. Ata ishin 30% më të fortë për shkak të përdorimit të fibrave dhe rrëshirës. Ekipi fitoi garën e tyre!
Pse na zgjidhni ne mbi të tjerët
Ja pse na zgjedhin kompanitë inteligjente:
- 28+ vite njohuri – Ne i kemi parë dhe rregulluar të gjitha problemet
- Ndihmë me porosi – Ne bëjmë atë që ju nevojitet, jo atë që është e lehtë për ne
- Punë e shpejtë – Ne ju marrim pjesë kur keni nevojë për to
- Çmime të drejta – Ne nuk harxhojmë para, ndaj paguani më pak
- Metodat e gjelbra – Ne përdorim më pak energji dhe më pak mbeturina
Sa kushton rruga jonë
Çmimet tona janë të drejta. Ja çfarë e bën koston të rritet ose të ulet në procesin e prodhimit:
- Sa pjesë ju nevojiten
- Sa të mëdha janë pjesët
- Sa të fortë duhet të jenë
- Sa shpejt keni nevojë për to
- Si duken
Ne do t'ju tregojmë çmimin përpara. Asnjë surprizë më vonë.
Si funksionon procesi ynë
- Ju na tregoni se çfarë keni nevojë
- Ne ju ndihmojmë të rregulloni dizajnin tuaj nëse është e nevojshme
- Ne zgjedhim mënyrën e duhur për ta bërë atë
- Ne bëjmë një pjesë provë që ju ta kontrolloni
- Ju thoni "po" ose kërkoni ndryshime
- Ne bëjmë të gjitha pjesët tuaja
- Ne kontrollojmë secilën prej tyre
- Ne i paketojmë ato të sigurta dhe i dërgojmë
- Ju merrni pjesë të shkëlqyera në kohë
Është kaq e thjeshtë!
Mënyra të reja për t'u përmirësuar
Ne vazhdojmë të gjejmë mënyra më të mira për të bërë pjesë me fibër karboni:
Fibra karboni me bazë linjine
Tani përdorim mbetjet e bimëve për të bërë fibër karboni. Kushton shumë më pak kur përdorni rrëshirë epokside. Përdor më pak vaj. Ajo funksionon po aq mirë.
Riciklimi i fibrave të karbonit
Tani mund të ripërdorim fibër karboni të vjetër. Kjo kursen para. Ajo ndihmon tokën. Pjesët janë ende të forta.
Metodat e mikrovalës
Mënyra jonë e re CARBOWAVE përdor 70% më pak energji. I bën pjesët po aq të mira. Është gjithashtu më i shpejtë.
Materiale të zgjuara
Ne po testojmë fibër karboni që mund të:
- T'ju tregoj kur është gati të prishet
- Ngroheni kur është ftohtë
- Rregulloni vetë çarjet e vogla
Mjetet që përdorim
Ne përdorim mjetet më të mira, duke përfshirë filamentin e avancuar të printimit 3D.
- Autoklava të nivelit të lartë – Për ngrohje perfekte
- Prerje kompjuterike – Për forma të sakta
- Skanera lazer – Për të kontrolluar secilën pjesë
- Ndihmës robotësh – Për të njëjtën punë çdo herë
- printera 3D – Për pjesë të testimit të shpejtë
Këto mjete na ndihmojnë të bëjmë pjesë më të mira. Ato na ndihmojnë të punojmë më shpejt duke përdorur materiale të përparuara të përbëra. Ato ndihmojnë në mbajtjen e çmimeve të drejta.
Çfarë thonë klientët tanë
"Ne provuam tre prodhues të tjerë përpara se të gjenim Scomp. Ata ia dolën mirë herën e parë. Tani ne i përdorim vetëm ata." – Kompani e pjesëve të makinave e specializuar në materialet e përbëra.
"Ata ndihmuan në rregullimin e dizajnit tonë për ta bërë atë më të fortë DHE më të lirë. Partner i madh!" – Prodhuesi i biçikletave
"Në kohë, me buxhet, pa dramë. Vetëm ajo që na duhej." – Blerësi i pjesëve të avionit
Si të Filloni
Gati për pjesë të shkëlqyera me fibër karboni? Ja se si të filloni:
- Na dërgoni dizajnin tuaj (ose na tregoni se çfarë ju nevojitet)
- Na tregoni sa pjesë ju nevojiten
- Na tregoni kur ju duhen
- Ne do t'ju tregojmë se si mund të ndihmojmë
Na dërgoni me email: [email protected] Na telefononi: +86-136 2619 1009
FAQ rreth punës sonë me fibra karboni
Pyetje: Sa kohë duhet për të bërë pjesë? Përgjigje: Pjesë të vogla, të thjeshta: 1-2 javë. Pjesë të mëdha, komplekse: 3-6 javë.
Pyetje: Cila është porosia juaj minimale? Përgjigje: Ne mund të bëjmë vetëm një pjesë nëse kjo është gjithçka që ju nevojitet!
Pyetje: A mund të më ndihmoni në rregullimin e dizajnit tim? A: Po! Ne e bëjmë këtë gjatë gjithë kohës për t'i bërë pjesët më të mira.
Pyetje: A bëni pjesë për dikë, përfshirë kompanitë e hapësirës ajrore? Përgjigje: Po - makina, biçikleta, aeroplanë, varka, pajisje sportive dhe më shumë.
Pyetje: A është fibra juaj e karbonit mjaft e fortë për gara? A: Po! Shumë ekipe garash përdorin pjesët tona.
Gati për të zgjidhur problemet tuaja të fibrave të karbonit?
Ndaloni të humbni kohë me pjesë të këqija. Ndaloni të paguani shumë. Mos i humbisni datat e nisjes.
Filloni të merrni pjesë perfekte me fibër karboni. Filloni të kurseni para duke kaluar te materialet e përbëra. Filloni t'i bëni klientët tuaj të lumtur.
Na kontaktoni sot dhe le të bëjmë diçka të mrekullueshme së bashku!