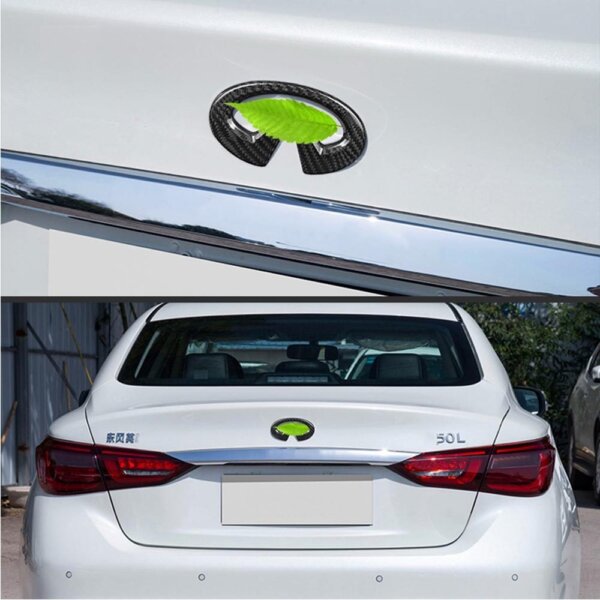
Fibra di carbonio secca vs carbonio umido: guida definitiva al confronto
Introduzione
I polimeri rinforzati con fibre di carbonio (CFRP) sono materiali compositi noti per il loro eccezionale rapporto resistenza/peso, rigidità e durata. Queste proprietà li rendono indispensabili in settori come quello aerospaziale, automobilistico e delle attrezzature sportive ad alte prestazioni. Quando si parla di "fibra di carbonio", in genere si parla di fogli di fibra di carbonio CFRP legati a una resina polimerica, solitamente epossidica.
Tuttavia, spesso si crea confusione sui termini "fibra di carbonio bagnata" E "fibra di carbonio asciutta". Un'idea sbagliata comune è che queste etichette descrivano la finitura della superficie: si pensa che "bagnato" significhi lucido e "asciutto" opaco. In realtà, i termini si riferiscono a due processi produttivi distinti utilizzato per laminare la fibra di carbonio con la resina.
Questo articolo chiarisce le differenze tra fibra di carbonio umida e secca, ne confronta la qualità e le prestazioni ed esplora le considerazioni pratiche per gli acquirenti. Che siate ingegneri, hobbisti o semplici curiosi di materiali avanzati, la comprensione di queste distinzioni vi aiuterà a prendere decisioni informate.
Processi di produzione
Fibra di carbonio bagnata
IL metodo di wet lay-up è l'approccio più tradizionale alla produzione di componenti in fibra di carbonio. Ecco come funziona:
- Applicazione manuale della resina: La resina epossidica liquida viene spennellata o spruzzata su fogli di fibra di carbonio asciutti collocati in uno stampo.
- Stratificazione: È possibile impilare più fogli per ottenere lo spessore desiderato.
- Stagionatura: La resina indurisce a temperatura ambiente o con un leggero calore, legando le fibre in una struttura solida.
Strumenti utilizzati: Pennelli, rulli o pistole a spruzzo per l'applicazione della resina; sacchetto sottovuoto (opzionale) per ridurre le bolle d'aria.
Professionisti:
- Costi ridotti per le attrezzature (non è necessaria l'autoclave).
- Flessibilità per progetti personalizzati o una tantum.
Contro:
- Distribuzione incoerente della resina, che porta a potenziali punti deboli.
- Maggiore rischio di difetti come sacche d'aria o polimerizzazione non uniforme.
Fibra di carbonio secca
Fibra di carbonio asciutta, o Fibra di carbonio preimpregnata (prepreg)utilizza un processo di produzione più avanzato:
- Tessuto preimpregnato: I fogli di fibra di carbonio sono pre-rivestiti con una quantità precisa di resina non polimerizzata in condizioni controllate in fabbrica.
- Lay-up: I fogli di preimpregnato vengono inseriti in uno stampo e coperti con un sacchetto sigillato sotto vuoto.
- Stagionatura: Il gruppo viene riscaldato in un autoclave (o in forno) ad alta pressione, garantendo un flusso uniforme di resina e un'adesione ottimale.
Vantaggi principali:
- Maggiore coerenza nella distribuzione della resina e nell'allineamento delle fibre.
- Rapporto resistenza/peso più elevato e minor numero di difetti.
Limitazioni:
- Richiede attrezzature costose (autoclavi).
- Meno accessibile per progetti su piccola scala o fai-da-te.
Differenze chiave in termini di qualità e prestazioni
Nella scelta tra fibra di carbonio umida e secca, la comprensione delle loro differenze strutturali e meccaniche è fondamentale per selezionare il materiale giusto per la vostra applicazione.
Coerenza e integrità strutturale
- Fibra di carbonio secca:
- La distribuzione della resina controllata in fabbrica garantisce saturazione uniforme delle fibre, eliminando i punti deboli.
- La polimerizzazione in autoclave si applica pressione e calore uniformiriducendo al minimo i vuoti o le aree ricche di resina.
- Fibra di carbonio bagnata:
- Rischi legati all'applicazione manuale della resina rivestimento incoerente, con conseguente disomogeneità della resistenza.
- Vulnerabile a bolle d'aria, punti secchi o ristagni di resina in eccessoche può compromettere la durata.
Rapporto forza-peso
- CF secco eccelle nelle applicazioni ad alte prestazioni grazie a:
- Rapporto fibra/resina ottimizzato (tipicamente 30-40% resina in peso).
- Più alto rigidità e resistenza alla trazione rispetto al CF bagnato.
- CF bagnato può sacrificare un po' di forza per la flessibilità:
- Il contenuto di resina spesso supera il 40%, aggiungendo peso inutile.
- Adatto per parti non strutturali dove la forza assoluta non è fondamentale.
Tassi di difettosità e longevità
- CF secco:
- Porosità prossima allo zero (<1%) grazie alla lavorazione in autoclave.
- Resistente a delaminazione e microfessure nel tempo.
- CF bagnato:
- Incline a vuoti (porosità 5-10%) senza sacchi a vuoto.
- Rischio più elevato di Degradazione UV se la resina non è completamente indurita.
Considerazioni pratiche per gli acquirenti
Confronto dei costi
Fattore | Fibra di carbonio secca | Fibra di carbonio bagnata |
---|---|---|
Costo iniziale | Alto ($100-$500/kg per il prepreg) | Basso ($20-$100/kg per i materiali) |
Attrezzatura necessaria | Autoclave ($50k–$1M+) | Strumenti di base (pennello, stampo) |
Intensità di lavoro | Basso (il prepreg è pre-ingegnerizzato) | Alto (abilità di stesura manuale) |
Scambi di opinioni:
- CF secco costo più elevato è giustificato per il settore aerospaziale o per le corse, dove il fallimento non è un'opzione.
- Il CF bagnato è economico per prototipi o parti decorative.
Applicazioni
- Il CF secco domina in:
- Aerospaziale: Fusoliera del Boeing 787 Dreamliner.
- Supercar: Telaio McLaren Monocage.
- Sport d'élite: Componenti di Formula 1, telai di biciclette di alta qualità.
- CF bagnato Adatti:
- Automotive personalizzato: Kit carrozzeria, rivestimenti interni.
- Progetti fai da te: Telai di droni, corpi di chitarre.
- Riparazioni: Ritocco di parti danneggiate del CF (ad esempio, scafi di imbarcazioni).
Durata e manutenzione
- Resistenza ambientale:
- La matrice di resina compatta del CF asciutto resiste meglio umidità, sostanze chimiche e raggi UV.
- La FC bagnata può richiedere rivestimenti protettivi per uso esterno.
- Riparabilità:
- Il CF bagnato è più facile da toppa con resina applicata a mano.
- Le riparazioni di CF a secco spesso richiedono reticolazione professionale in autoclave.
Sfatare i miti comuni sulla fibra di carbonio
La fibra di carbonio è circondata da idee sbagliate, soprattutto per quanto riguarda i metodi di produzione a umido e a secco. Vediamo di chiarire due miti principali:
Mito 1: "La fibra di carbonio bagnata è lucida, quella asciutta è opaca".
- La realtà: I termini "umido" e "secco" si riferiscono a solo al processo di produzionenon la finitura superficiale.
- Opzioni di finitura: Entrambi i tipi possono raggiungere lucido, opaco o satinato finiture in base a:
- Resina di finitura (ad esempio, vernice trasparente resistente ai raggi UV per ottenere una maggiore lucentezza).
- Additivi (ad esempio, agenti opacizzanti mescolati all'epossidica).
- Esempio: Un cofano in fibra di carbonio asciutto può essere lucidato a specchio, mentre la fibra di carbonio bagnata può essere lasciata opaca per ottenere un look stealth.
Mito 2: "La fibra di carbonio asciutta è sempre migliore".
- La realtà: Il CF secco supera le prestazioni in applicazioni ad alte sollecitazioni, ma il CF bagnato presenta dei vantaggi:
- Costo-efficacia: Ideale per prototipi unici o parti non portanti (ad esempio, pannelli decorativi).
- Flessibilità: Più facile da modellare a mano forme complesse senza vincoli di autoclave.
- Riparabilità: La stratificazione a umido è più semplice per riparazioni sul campo (ad esempio, la riparazione di una carenatura di una moto incrinata).
- Quando scegliere il CF umido:
- Progetti a budget limitato.
- Produzione di piccole serie in cui l'attrezzaggio per il CF a secco non è praticabile.
Fattori ambientali e fai-da-te
Sostenibilità della produzione di fibra di carbonio
Fattore | Fibra di carbonio secca | Fibra di carbonio bagnata |
---|---|---|
Uso dell'energia | Alto (l'autoclave consuma ~50 kWh per pezzo) | Basso (polimerizza a temperatura ambiente) |
Rifiuti di resina | Minimo (quantità precise di prepreg) | La resina in eccesso viene spesso scartata |
Riciclabilità | Impegnativo (epossidici termoindurenti) | Stesse limitazioni, ma alcune bioresine emergenti |
Progressi eco-compatibili:
- CF riciclato: Alcuni produttori triturano le fibre di scarto per riutilizzarle in parti non strutturali.
- Resine a base biologica: Epossidici sperimentali di origine vegetale riducono la dipendenza dai prodotti petrolchimici.
Fattibilità del fai da te
- Fibra di carbonio bagnata:
- Per i principianti: Richiede solo strumenti di base (pennelli, stampi e resina).
- Progetti popolari: Rivestimenti personalizzati per auto, telai per droni o armature per cosplay.
- Tutorial: Le guide online per il wet lay-up su piccola scala sono numerose.
- Fibra di carbonio secca:
- Barriere: Le autoclavi sono costo proibitivo per hobbisti ($50k+).
- Soluzioni: Alcuni usi preimpregnati polimerizzati in forno (limitatamente alle piccole parti).
- Laboratori comunitari: Gli spazi maker condivisi offrono talvolta l'accesso all'autoclave.
Nota sulla sicurezza:
- Lavorare sempre in un area ben ventilata-I fumi dell'epossidico sono tossici.
- Indossare guanti e occhiali di protezione per evitare irritazioni cutanee dovute alla resina non polimerizzata.
Applicazioni industriali: Dove brillano le fibre di carbonio umide e secche
Le proprietà uniche della fibra di carbonio l'hanno resa indispensabile nei settori ad alte prestazioni. Ecco come le fibre di carbonio umide e secche vengono utilizzate nelle applicazioni reali:
Automotive: Precisione e praticità
La fibra di carbonio secca domina le prestazioni di fascia alta
- Componenti strutturali: Utilizzato in telaio monoscocca (ad esempio, McLaren Senna, Ferrari SF90) per ottenere la massima rigidità e risparmio di peso.
- Parti critiche: Alberi di trasmissione, bracci delle sospensioni e componenti dei freni traggono vantaggio dalla consistenza del CF secco.
- Corsa: I team di Formula 1 si affidano ai preimpregnati polimerizzati in autoclave per i componenti aerodinamici.
Fibra di carbonio umida per la personalizzazione e l'efficienza dei costi
- Kit corpo: I cofani, gli spoiler e i parafanghi aftermarket utilizzano spesso il wet lay-up per motivi di convenienza.
- Rifiniture interne: Pannelli decorativi del cruscotto o accenti delle porte in cui non è richiesta una resistenza estrema.
- Restauri: Riparazioni di auto d'epoca in cui l'estetica d'epoca è più importante della perfetta distribuzione della resina.
Caso di studio: Mercedes-AMG
- CF secco: elementi strutturali come il Tubo di torsione della AMG GT.
- CF bagnato: opzionale pacchetti esterni in fibra di carbonio per l'attrattiva visiva.
Aerospazio: Dove ogni grammo conta
- La fibra di carbonio asciutta è lo standard
- Strutture aeronautiche: Le fusoliere dei Boeing 787 e degli Airbus A350 utilizzano preimpregnati polimerizzati in autoclave per la resistenza alla fatica.
- Veicolo spaziale: I supporti dello scudo termico di SpaceX Dragon sfruttano la stabilità termica del CF secco.
- I ruoli di nicchia della fibra di carbonio umida
- Prototipazione: Mockup rapidi e a basso costo per testare l'aerodinamica.
- Parti non critiche: Divisori per cabine o contenitori in cui il peso non è una preoccupazione primaria.
Conclusione: Scegliere la fibra di carbonio giusta per le proprie esigenze
Riepilogo delle principali differenze
Fattore | Fibra di carbonio secca | Fibra di carbonio bagnata |
---|---|---|
Il migliore per | Applicazioni critiche per le prestazioni | Progetti personalizzati e sensibili ai costi |
Costo | Alto (attrezzature + materiali) | Basso (sono necessari strumenti minimi) |
Livello di abilità | Necessità di competenze industriali | Fai-da-te |
Tendenze future nella tecnologia della fibra di carbonio
- Layup automatizzato: Robot per la laminazione a umido per ridurre l'errore umano (ad esempio, la produzione di CFRP della BMW).
- Preimpregnati fuori autoclave (OoA): Nuove resine che polimerizzano in forno, abbassando la barriera d'ingresso della CF a secco.
- Soluzioni sostenibili:
- Termoplastici riciclabili: Alternative alle epossidiche tradizionali (ad esempio, la resina Elium di Arkema).
- Riciclaggio a ciclo chiuso: Aziende come Toray Industries che recuperano il CF dagli aerei fuori uso.
Raccomandazione finale
- Scegliete la fibra di carbonio a secco se: È necessario prestazione massima e dispongono di un budget per il trattamento in autoclave.
- Scegliete la fibra di carbonio bagnata se: Dare priorità flessibilità, convenienza o personalizzazione fai-da-te.
La fibra di carbonio continua a evolversi, colmando il divario tra ingegneria high-tech e artigianato accessibile. Sia che stiate costruendo un'auto da corsa o un telaio di bicicletta personalizzato, la comprensione di queste opzioni vi permetterà di sfruttare al meglio questo materiale rivoluzionario.
Avete un progetto in mente? Condividete le vostre domande qui sotto: saremo lieti di aiutarvi!