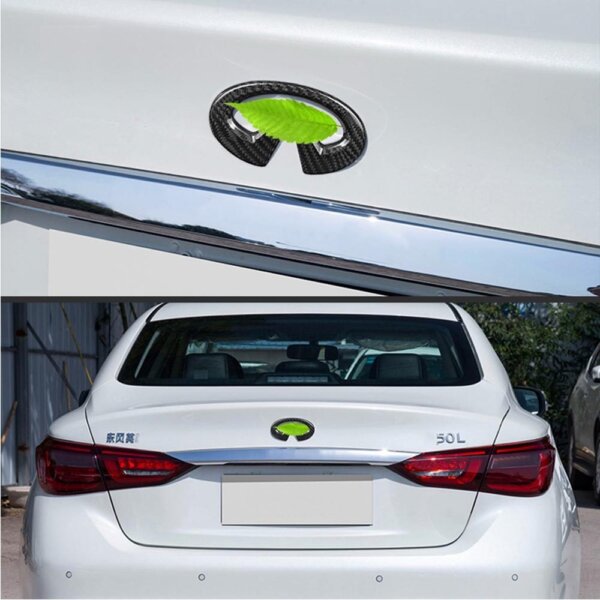
Trockene Kohlefaser vs. nasse Kohlefaser: Ultimativer Vergleichsleitfaden
Einführung
Kohlenstofffaserverstärkte Polymere (CFK) sind Verbundwerkstoffe, die für ihr außergewöhnliches Verhältnis von Festigkeit zu Gewicht, Steifigkeit und Haltbarkeit bekannt sind. Diese Eigenschaften machen sie in Branchen wie der Luft- und Raumfahrt, der Automobilindustrie und bei Hochleistungssportgeräten unverzichtbar. Wenn man von "Kohlefasern" spricht, meint man in der Regel CFK - Kohlefaserplatten, die mit einem Polymerharz, meist Epoxidharz, verbunden sind.
Allerdings kommt es häufig zu Verwirrung bei den Begriffen "Nasse Kohlefaser" Und "trockene Kohlefaser". Ein weit verbreiteter Irrglaube ist, dass diese Bezeichnungen die Oberflächenbeschaffenheit beschreiben - in der Annahme, dass "nass" für glänzend und "trocken" für matt steht. In Wirklichkeit beziehen sich die Begriffe auf zwei unterschiedliche Herstellungsverfahren für die Laminierung von Kohlenstofffasern mit Harz.
Dieser Artikel erläutert die Unterschiede zwischen nasser und trockener Kohlefaser, vergleicht ihre Qualität und Leistung und geht auf praktische Überlegungen für Käufer ein. Ganz gleich, ob Sie Ingenieur, Bastler oder einfach nur neugierig auf fortschrittliche Materialien sind, das Verständnis dieser Unterschiede wird Ihnen helfen, fundierte Entscheidungen zu treffen.
Herstellungsverfahren
Nasse Kohlenstofffaser
Der Nassauflegeverfahren ist die traditionellere Methode zur Herstellung von Kohlefaserteilen. Und so funktioniert's:
- Manuelles Auftragen des Harzes: Flüssiges Epoxidharz wird mit einem Pinsel oder durch Sprühen auf trockene Kohlefaserplatten aufgetragen, die in eine Form gelegt werden.
- Schichtung: Mehrere Platten können gestapelt werden, um die gewünschte Dicke zu erreichen.
- Aushärtung: Das Harz härtet bei Raumtemperatur oder bei leichter Hitze aus und verbindet die Fasern zu einer festen Struktur.
Verwendete Werkzeuge: Pinsel, Rollen oder Spritzpistolen zum Auftragen des Harzes; Vakuumbeutel (optional) zur Reduzierung von Luftblasen.
Vorteile:
- Geringe Ausrüstungskosten (kein Autoklav erforderlich).
- Flexibilität für individuelle oder einmalige Projekte.
Nachteile:
- Uneinheitliche Harzverteilung, was zu potenziellen Schwachstellen führt.
- Höheres Risiko von Mängeln wie Lufteinschlüssen oder ungleichmäßiger Aushärtung.
Trockene Kohlefaser
Trockene Kohlefaser, oder Prepreg (vorimprägnierte) Kohlenstofffaserverwendet ein fortschrittlicheres Herstellungsverfahren:
- Prepreg-Gewebe: Kohlefaserplatten werden unter werkseitig kontrollierten Bedingungen mit einer präzisen Menge an unausgehärtetem Harz vorbeschichtet.
- Korbleger: Die Prepregplatten werden in eine Form gelegt und mit einem vakuumversiegelten Beutel abgedeckt.
- Aushärtung: Die Baugruppe wird in einem Autoklav (oder Ofen) unter hohem Druck, wodurch ein gleichmäßiger Harzfluss und eine optimale Verklebung gewährleistet werden.
Die wichtigsten Vorteile:
- Hervorragende Konsistenz bei der Harzverteilung und Faserausrichtung.
- Höheres Verhältnis von Festigkeit zu Gewicht und weniger Defekte.
Beschränkungen:
- Erfordert teure Ausrüstung (Autoklaven).
- Weniger zugänglich für kleine oder DIY-Projekte.
Hauptunterschiede in Qualität und Leistung
Bei der Wahl zwischen nasser und trockener Kohlefaser ist das Verständnis ihrer strukturellen und mechanischen Unterschiede entscheidend für die Auswahl des richtigen Materials für Ihre Anwendung.
Konsistenz und strukturelle Integrität
- Trockene Kohlefaser:
- Die werkseitig kontrollierte Harzverteilung gewährleistet gleichmäßige Sättigung der Fasern, wodurch Schwachstellen beseitigt werden.
- Die Aushärtung im Autoklaven erfolgt gleichmäßiger Druck und Hitzeund die Minimierung von Hohlräumen oder harzreichen Bereichen.
- Nasse Kohlenstofffaser:
- Risiken der manuellen Harzapplikation uneinheitliche Beschichtungwas zu einer ungleichmäßigen Festigkeit führt.
- Anfällig für Luftblasen, trockene Stellen oder überschüssige Harzansammlungenwas die Haltbarkeit beeinträchtigen kann.
Verhältnis Stärke/Gewicht
- Trockener CF zeichnet sich bei Hochleistungsanwendungen durch folgende Eigenschaften aus:
- Optimiertes Faser-zu-Harz-Verhältnis (typischerweise 30-40% Harz nach Gewicht).
- Höher Steifigkeit und Zugfestigkeit als feuchter CF.
- Nasses CF kann etwas Kraft für Flexibilität opfern:
- Der Harzgehalt übersteigt oft 40%, was zu unnötigem Gewicht führt.
- Geeignet für nicht-strukturelle Teile wo die absolute Stärke nicht entscheidend ist.
Fehlerraten & Langlebigkeit
- Trockener CF:
- Nahezu keine Porosität (<1%) aufgrund der Verarbeitung im Autoklaven.
- Widerstandsfähig gegen Delamination und Mikrorisse im Laufe der Zeit.
- Nasses CF:
- Anfällig für Hohlräume (5-10% Porosität) ohne Vakuumverpackung.
- Höheres Risiko von UV-Zersetzung wenn das Harz nicht vollständig ausgehärtet ist.
Praktische Erwägungen für Käufer
Kostenvergleich
Faktor | Trockene Kohlefaser | Nasse Kohlenstofffaser |
---|---|---|
Vorabkosten | Hoch ($100-$500/kg für Prepreg) | Niedrig ($20-$100/kg für Materialien) |
Benötigte Ausrüstung | Autoclave ($50k–$1M+) | Grundlegende Werkzeuge (Pinsel, Form) |
Arbeitsintensität | Niedrig (Prepreg ist vorgefertigt) | Hoch (manuelle Legetechniken) |
Abwägungen:
- Trockene CF's höhere Kosten ist in der Luft- und Raumfahrt oder im Rennsport gerechtfertigt, wo ein Versagen keine Option ist.
- Nasses CF ist budgetfreundlich für Prototypen oder dekorative Teile.
Anwendungen
- Trockener CF dominiert in:
- Luft- und Raumfahrt: Rumpf der Boeing 787 Dreamliner.
- Supersportwagen: McLaren Monocage Fahrgestell.
- Elitesport: Formel-1-Komponenten, hochwertige Fahrradrahmen.
- Nasse CF-Passungen:
- Custom Automotive: Karosserie-Kits, Innenverkleidung.
- DIY-Projekte: Drohnenrahmen, Gitarrenkörper.
- Reparaturen: Ausbessern beschädigter CF-Teile (z. B. Bootsrümpfe).
Langlebigkeit und Wartung
- Umweltresistenz:
- Die dichte Harzmatrix des trockenen CF widersteht besser Feuchtigkeit, Chemikalien und UV-Strahlung.
- Nasses CF kann erfordern Schutzbeschichtungen für die Verwendung im Freien.
- Reparierbarkeit:
- Nasses CF ist leichter zu Patch mit handverlegtem Harz.
- Trockene CF-Reparaturen erfordern oft professionelle Nachhärtung im Autoklaven.
Entlarvung gängiger Mythen über Kohlefaser
Um Kohlefaser ranken sich viele Irrtümer, vor allem in Bezug auf Nass- und Trockenfertigungsverfahren. Lassen Sie uns mit zwei wichtigen Mythen aufräumen:
Mythos 1: "Nasse Kohlefaser ist glänzend, trockene Kohlefaser ist matt"
- Realität: Die Begriffe "nass" und "trocken" beziehen sich auf nur für den Herstellungsprozessund nicht die Oberflächenbeschaffenheit.
- Ausführungsoptionen: Beide Typen können Folgendes erreichen glänzend, matt oder satiniert je nach Ausführung:
- Topcoat-Harz (z. B. UV-beständiger Klarlack für Glanz).
- Zusatzstoffe (z. B. in Epoxidharz eingemischte Mattierungsmittel).
- Beispiel: Eine trockene Karbonfaserhaube kann auf Hochglanz poliert werden, während nasse Karbonfaser für ein unauffälliges Aussehen matt belassen werden kann.
Mythos 2: "Trockene Kohlefaser ist immer besser"
- Realität: Trockener CF schneidet besser ab in hochbeanspruchte Anwendungenaber nasser CF hat Vorteile:
- Kosten-Wirksamkeit: Ideal für einmalige Prototypen oder nicht tragende Teile (z. B. Zierplatten).
- Flexibilität: Einfacher zu handgeformte komplexe Formen ohne Autoklaven-Zwänge.
- Reparierbarkeit: Das Nassauflegen ist einfacher für Feldreparaturen (z. B. die Reparatur einer gerissenen Motorradverkleidung).
- Wann sollte man Wet CF wählen?:
- Projekte mit begrenztem Budget.
- Kleinserienproduktion, bei der die Herstellung von Werkzeugen für trockenen CF unpraktisch ist.
Umwelt- und DIY-Faktoren
Nachhaltigkeit der Kohlenstofffaserproduktion
Faktor | Trockene Kohlefaser | Nasse Kohlenstofffaser |
---|---|---|
Energieverbrauch | Hoch (Autoklav verbraucht ~50 kWh pro Teil) | Niedrig (härtet bei Raumtemperatur aus) |
Harzabfälle | Minimal (genaue Prepreg-Mengen) | Überschüssiges Harz wird oft entsorgt |
Wiederverwertbarkeit | Anspruchsvoll (duroplastische Epoxide) | Dieselben Einschränkungen, aber einige neue Bioharze |
Umweltverträgliche Fortschritte:
- Recycelter CF: Einige Hersteller zerkleinern Altfasern zur Wiederverwendung in nicht-strukturellen Teilen.
- Biobasierte Harze: Experimentelle Epoxide auf pflanzlicher Basis verringern die Abhängigkeit von Petrochemikalien.
DIY Durchführbarkeit
- Nasse Kohlenstofffaser:
- Einsteigerfreundlich: Erfordert nur Grundwerkzeuge (Pinsel, Gussformen und Harz).
- Beliebte Projekte: Individuelle Autoverkleidungen, Drohnenrahmen oder Cosplay-Rüstungen.
- Anleitungen: Es gibt zahlreiche Online-Leitfäden für die Nassverlegung in kleinem Maßstab.
- Trockene Kohlefaser:
- Barrieren: Autoklaven sind unerschwinglich für Bastler ($50k+).
- Umgehungen: Gewisse Verwendung ofengehärtete Prepregs (beschränkt auf kleine Teile).
- Gemeinschaftslaboratorien: Gemeinsam genutzte Makerspaces bieten manchmal Zugang zu Autoklaven.
Sicherheitshinweis:
- Arbeiten Sie immer in einer gut belüfteter Raum-Epoxiddämpfe sind giftig.
- Tragen Sie Handschuhe und Schutzbrille um Hautreizungen durch unausgehärtetes Harz zu vermeiden.
Industrielle Anwendungen: Wo nasse und trockene Carbonfasern glänzen
Die einzigartigen Eigenschaften von Kohlenstofffasern haben sie in der Hochleistungsindustrie unverzichtbar gemacht. Hier erfahren Sie, wie nasse und trockene Kohlenstofffasern in der Praxis eingesetzt werden:
Automobilindustrie: Präzision vs. Zweckmäßigkeit
Trockene Kohlefaser dominiert High-End-Leistung
- Strukturelle Komponenten: Verwendet in Monocoque-Fahrwerk (z. B. McLaren Senna, Ferrari SF90) für maximale Steifigkeit und Gewichtseinsparung.
- Kritische Teile: Antriebswellen, Querlenker und Bremskomponenten profitieren von der Beständigkeit des trockenen CF.
- Rennen: Formel-1-Teams setzen auf autoklavgehärtetes Prepreg für aerodynamische Komponenten.
Nasse Kohlefaser für Individualisierung und Kosteneffizienz
- Karosserie-Kits: Bei Motorhauben, Spoilern und Kotflügeln für den Nachrüstmarkt wird aus Kostengründen häufig das Wet-Lay-up-Verfahren angewendet.
- Innenausstattung: Dekorative Armaturenbretter oder Türakzente, bei denen keine extreme Festigkeit erforderlich ist.
- Wiederherstellungen: Oldtimer-Reparaturen, bei denen die Ästhetik eines Oldtimers wichtiger ist als eine perfekte Harzverteilung.
Fallstudie: Mercedes-AMG
- Trockener CF: Strukturelle Elemente wie die AMG GTs Drehmomentrohr.
- Wet CF: Optional Kohlefaser-Exterieurpakete für visuelle Attraktivität.
Luft- und Raumfahrt: Wo jedes Gramm zählt
- Trockene Kohlefaser ist der Standard
- Luftfahrzeug-Strukturen: In den Rümpfen der Boeing 787 und des Airbus A350 werden autoklavgehärtete Prepregs verwendet, um die Ermüdungsfestigkeit zu erhöhen.
- Raumfahrzeug: Die Hitzeschildbefestigung von SpaceX Dragon nutzt die thermische Stabilität von Dry CF.
- Nischenfunktionen der nassen Kohlefaser
- Prototyping: Schnelle, kostengünstige Modelle für Aerodynamiktests.
- Nicht-kritische Teile: Kabinenteiler oder Aufbewahrungskästen, bei denen das Gewicht keine Rolle spielt.
Schlussfolgerung: Die Wahl der richtigen Kohlefaser für Ihre Bedürfnisse
Zusammenfassung der Hauptunterschiede
Faktor | Trockene Kohlefaser | Nasse Kohlenstofffaser |
---|---|---|
Am besten für | Leistungskritische Anwendungen | Kundenspezifische, kostensensitive Projekte |
Kosten | Hoch (Ausrüstung + Material) | Gering (minimale Werkzeuge erforderlich) |
Fähigkeitsstufe | Industrielles Fachwissen erforderlich | DIY-freundlich |
Zukünftige Trends in der Kohlefasertechnologie
- Automatisierte Verlegung: Roboter für die Nassverlegung zur Verringerung menschlicher Fehler (z. B. in der CFK-Produktion von BMW).
- Out-of-Autoclave (OoA) Prepregs: Neue Harze, die im Ofen aushärten, senken die Einstiegshürde für trockenes CF.
- Nachhaltige Lösungen:
- Recycelbare Thermoplaste: Alternativen zum herkömmlichen Epoxidharz (z. B. Elium-Harz von Arkema).
- Recycling im geschlossenen Kreislauf: Unternehmen wie Toray Industries gewinnen CFK aus ausrangierten Flugzeugen zurück.
Abschließende Empfehlung
- Wählen Sie Dry Carbon Fiber, wenn: Sie benötigen maximale Leistung und über das nötige Budget für die Autoklavenbehandlung verfügen.
- Wählen Sie Wet Carbon Fiber, wenn: Sie setzen Prioritäten Flexibilität, Erschwinglichkeit, oder DIY-Anpassung.
Kohlefaser entwickelt sich ständig weiter und schließt die Lücke zwischen Hightech-Technik und handwerklichem Können. Ganz gleich, ob Sie einen Rennwagen oder einen individuellen Fahrradrahmen bauen - wenn Sie diese Optionen kennen, können Sie das Beste aus diesem revolutionären Material herausholen.
Haben Sie ein Projekt im Sinn? Teilen Sie uns Ihre Fragen mit - wir helfen Ihnen gerne weiter!