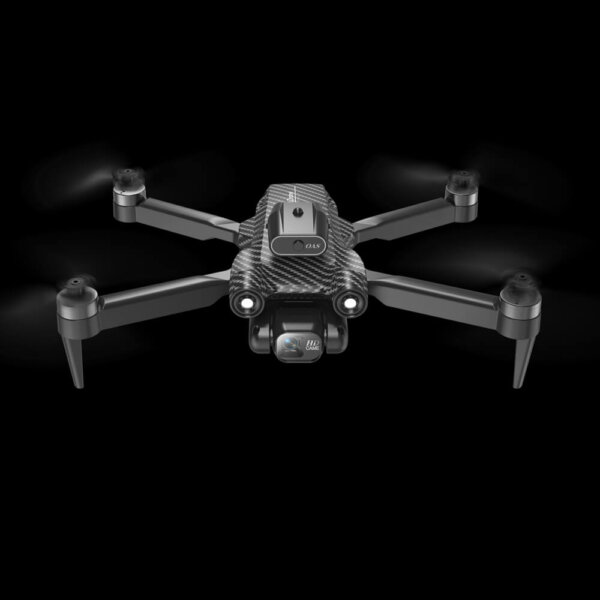
Comment fabriquer un moule en fibre de carbone : des étapes faciles pour des pièces solides
Es-tu bloqué avec des moules métalliques trop chers ? détester Vous attendez vos pièces depuis des semaines ? Votre équipe est-elle frustré par des outils lourds et difficiles à manipuler ?
Nous savons ce que vous ressentez. Depuis plus de 28 ans, notre équipe aide les entreprises à résoudre ces problèmes précis.
Le gros problème des moules traditionnels
Moules métalliques traditionnels blesser votre entreprise de trois manières :
- Ils coûtent trop d'argent ($5,000-$20,000)
- Ils prennent trop de temps (4 à 8 semaines)
- Ils sont trop lourd se déplacer facilement
Cela signifie que vous perdez de l’argent, que vous ne respectez pas les délais et que vous fatiguez vos employés.
Pourquoi cela empire
Lorsque vous continuez à utiliser d’anciennes méthodes de moulage :
- Ton concurrents mettre les pièces sur le marché plus rapidement
- Ton marges bénéficiaires rétrécir
- Ton ouvriers se fatiguer à déplacer des moules lourds
- Ton clients aller ailleurs
Chaque jour où vous vous en tenez à d’anciens types de moisissures, ces problèmes s’aggravent.
La solution intelligente : les moules en fibre de carbone
Nos moules en fibre de carbone résolvent tous ces problèmes à la fois :
- Économisez de l'argent (les coûts baissent de 85%)
- Gagnez du temps (obtenez des moisissures en quelques jours, pas en quelques semaines)
- Économiser de l'énergie (léger mais super résistant)
Laissez-moi vous montrer comment fabriquer ces incroyables moules étape par étape.
Ce dont vous avez besoin pour commencer
Vous avez besoin de ces outils simples :
Outil | Ce qu'il fait | Où l'obtenir |
---|---|---|
Filament PVA | Réalise votre forme imprimée en 3D | Boutiques en ligne |
Tissu en fibre de carbone | Donne de la force | Notre boutique |
Résine époxy | Maintient tout ensemble | Notre boutique |
Kit de sac sous vide | Élimine les bulles d'air | Notre boutique |
Étape 1 : Concevez la forme de votre moule
Tout d’abord, faites un plan pour votre moule :
- Utilisez Fusion 360 pour dessiner votre pièce
- Ajouter lignes de division du moule où les pièces se sépareront
- Vérifiez que les formes peuvent être supprimées facilement
Conseil de pro: Créez des formes aux courbes douces. Les angles vifs rendent les moules difficiles à utiliser.
Étape 2 : Choisissez votre type de moule
Choisissez le meilleur type de moule pour votre travail :
Moules imprimés en 3D ($300-$1,500)
- Idéal pour : les petites pièces, les essais
- Prêt dans : 3 à 7 jours
- Bon pour : jusqu'à 50 pièces
Moules de superposition de fibres de carbone ($1,000-$5,000)
- Idéal pour : Pièces moyennes
- Prêt dans : 2 à 3 semaines
- Bon pour : jusqu'à 100 pièces
Moules à noyau métallique + coque en carbone
- Idéal pour : Haute chaleur, haute pression
- Prêt dans : 3 semaines
- Bon pour : des centaines de pièces
La plupart de nos fibre de carbone personnalisée les pièces commencent par le type #1 ou #2.
Étape 3 : Imprimez votre moule de base
Si vous utilisez un moule imprimé en 3D :
- Chargez le filament PVA dans votre imprimante 3D
- Définissez les paramètres d'impression sur des couches de 0,1 mm pour une finition lisse
- Imprimez à 215°C pour de meilleurs résultats
- Laisser refroidir complètement avant de manipuler
AvertissementVérifiez que votre impression ne présente pas de bosses ni de trous. Ils apparaîtront sur votre pièce finale !
Étape 4 : Préparez la surface de votre moule
Préparez maintenant votre moule pour le carbone :
- Poncer avec du papier de verre grain 400
- Essuyer avec de l'alcool
- Appliquer agent de démoulage trois fois
- Laisser sécher 20 minutes entre les couches
Cette étape est très important! Sautez-le et votre rôle restera gravé à jamais.
Étape 5 : Coupez votre tissu en fibre de carbone
Il est temps de préparer votre carbone :
- Utilisez des ciseaux pointus conçus pour le carbone
- Coupez des morceaux de 1 pouce plus grands que votre moule
- Gardez 3 couches pour 1 mm d'épaisseur
- Conserver à plat jusqu'à utilisation.
Notre fibre de carbone Le tissu se décline en différents motifs de tissage. Le tissage sergé est le plus adapté à la plupart des moules.
Étape 6 : Mélangez votre résine
Préparez votre résine :
- Mélanger la résine et le durcisseur (vérifiez le ratio de votre marque)
- Remuer lentement pendant 3 minutes
- Maintenez la température entre 20 et 30 °C pour un meilleur débit
Astuce: Laissez refroidir votre résine au réfrigérateur pendant 30 minutes avant de mélanger si la pièce est chaude.
Étape 7 : Posez votre fibre de carbone
Construisez maintenant votre moule :
- Appliquer la résine au pinceau sur la surface du moule
- Poser la première couche de fibre de carbone
- Appuyez avec la brosse pour éliminer l'air
- Ajouter plus de résine
- Répéter avec toutes les couches
Travaillez vite mais avec précaution. Croisez les directions des fibres pour plus de solidité.
Étape 8 : Mettre le moule sous vide
Cette étape rend votre moule solide :
- Placer le moule dans un sac sous vide
- Sceller tous les bords
- Connecter la pompe à vide
- Pression de traction -0,8 bar
- Vérifiez les fuites
- Faire fonctionner le vide pendant au moins 2 heures
Le vide expulse l'air et l'excès de résine, ce qui renforce votre moule.
Étape 9 : Laissez sécher
Attendez que votre moule durcisse :
- Conserver à température ambiante pendant 24 heures
- Pour une meilleure résistance, post-durcissement à 60°C pendant 2 heures
- Attendre qu'il soit complètement refroidi avant de le retirer
Important: Ne vous précipitez pas ! La résistance maximale est obtenue avec un temps de séchage complet.
Étape 10 : Retirer et terminer
Dernières étapes :
- Retirez délicatement le moule de la base
- Coupez l'excédent avec un outil de coupe
- Bords de sable lisses
- Appliquer l'agent de démoulage final
Votre moule en fibre de carbone est maintenant prêt à fabriquer des pièces !
Résultats réels : étude de cas
Regardez ces vrais résultats de notre boutique :
Moule d'admission d'air de voiture
- Ancienne méthode : le moule en métal coûte $15 000, prend 6 semaines
- Notre méthode : Le moule en fibre de carbone coûte $1 200, a pris 5 jours
- Économies:$13,800 et 5 semaines de temps
Le constructeur automobile pourrait tester ses modèles 5 fois plus vite ! Il utilise désormais notre méthode pour tous ses nouveaux modèles. voiture en fibre de carbone parties.
Problèmes courants et solutions rapides
Même les pros ont parfois des problèmes :
Problème | Cause | Réparez-le rapidement |
---|---|---|
Bulles dans la moisissure | Lay-up trop rapide | Travaillez plus lentement, utilisez l'aspirateur plus longtemps |
Moisissure collante | Pas assez d'agent de démoulage | Appliquez 5 couches la prochaine fois |
Points faibles | Résine inégale | Utiliser la méthode d'infusion de résine |
Gauchissement | Trop de chaleur trop vite | Laisser durcir d'abord à température ambiante |
Pourquoi nos moules en fibre de carbone sont gagnants
Nos moules surpassent les moules métalliques de plusieurs manières :
- Coût:85% moins cher que le métal
- Vitesse:Prêt en quelques jours, pas en semaines
- Poids: 70% plus léger que le métal
- Transfert de chaleur:Chauffage/refroidissement plus uniforme
- Sentir: Chaud au toucher (les ouvriers adorent ça !)
Beaucoup moto en fibre de carbone les pièces sont désormais fabriquées avec nos méthodes de moulage.
Conseils avancés issus de nos 28 années d'expérience
Envie de réaliser des moules de niveau professionnel ? Essayez ceux-ci :
- Mélanger les matériaux du moule – Ajouter des premières couches de fibre de verre pour réaliser des économies
- Fabriquer des moules modulaires – Construisez des sections qui s’emboîtent pour les grandes pièces
- Utiliser du gel coat – Appliquer un revêtement spécial pour une finition ultra lisse
- Ajouter des éléments chauffants – Fils intégrés pour un durcissement contrôlé
- Créer des modèles principaux – Créer un moule parfait pour faire de nombreuses copies
Pourquoi nous choisir comme partenaire en fibre de carbone
Nous apportons plus de 28 ans de savoir-faire à vos projets :
- Solutions personnalisées pour n'importe quelle partie
- Délai d'exécution rapide fois
- Contrôle de qualité à chaque étape
- Économies de coûts vous a été transmis
- Guichet unique pour tous les besoins en carbone
Commencez dès aujourd'hui
Prêt à essayer les moules en fibre de carbone ? Voici comment :
- Envoyez-nous votre conception de pièce
- Nous vous suggérerons le meilleur type de moule
- Obtenez un devis gratuit dans les 24 heures
- Approuvez et nous commençons tout de suite
- Recevez votre moule en quelques jours
Ne perdez plus de temps et d'argent avec des moules obsolètes. Rejoignez les nombreuses entreprises qui font confiance à notre expertise en fibre de carbone.
Appelez-nous au +86-136 2619 1009 ou envoyez un e-mail à [email protected] dès aujourd'hui !