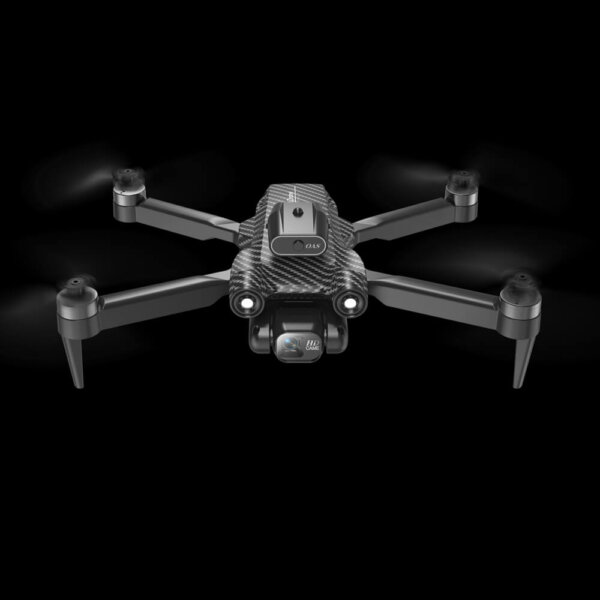
カーボンファイバー型の作り方: 簡単な手順で強力なパーツを作る
あなたは 立ち往生 コストが高すぎる金属金型で? 嫌い 部品を何週間も待っていますか?あなたのチームは イライラした 重くて扱いにくい道具で?
私たちはその気持ちがよくわかります。28 年以上にわたり、私たちのチームはまさにこれらの問題を解決するために企業を支援してきました。
従来の金型の大きな問題
伝統的な金属金型 傷つく ビジネスに3つの方法:
- 費用は お金が多すぎる ($5,000-$20,000)
- 彼らは 時間が多すぎる (4~8週間)
- 彼らです 重すぎる 簡単に動く
これは、お金を失い、期限に間に合わず、従業員を疲れさせることを意味します。
なぜこれが悪化するのか
古い金型方法を使い続けると、次のようになります。
- あなたの 競争相手 部品をより早く市場に投入する
- あなたの 利益率 縮む
- あなたの 労働者 重い金型を動かすのに疲れる
- あなたの 顧客 他の場所に行く
古いタイプの金型を使い続けるほど、これらの問題は大きくなります。
スマートソリューション: カーボンファイバー金型
当社のカーボンファイバー金型は、これらの問題をすべて一度に解決します。
- お金を節約する (コストは85%減少)
- 時間を節約 (数週間ではなく数日で型が手に入ります)
- エネルギーを節約する (軽量ですが超強力)
これらの素晴らしい型の作り方を段階的に説明しましょう。
始めるために必要なもの
必要なのは、次の簡単なツールです。
道具 | 何をするのか | 入手先 |
---|---|---|
PVAフィラメント | 3Dプリントした形状を作る | オンラインストア |
カーボンファイバークロス | 強さを与える | 当店 |
エポキシ樹脂 | すべてをまとめる | 当店 |
真空バッグキット | 気泡を除去します | 当店 |
ステップ1: 型の形状を設計する
まず、型の計画を立てます。
- Fusion 360を使用してパーツを描画する
- 追加 金型分割線 部品が分離する場所
- 図形が簡単に削除できることを確認する
プロのヒント: なだらかな曲線で形を作ります。角が鋭いと型が使いにくくなります。
ステップ2: 型の種類を選択する
作業に最適な金型タイプを選択してください:
3Dプリント金型 ($300-$1,500)
- 最適な用途: 小型部品、テスト実行
- 準備完了まで: 3~7 日
- 適しているもの: 最大50個の部品
カーボンファイバーレイアップモールド ($1,000-$5,000)
- 最適な用途: 中型部品
- 準備期間: 2~3 週間
- 適しているもの: 最大100個の部品
メタルコア+カーボンシェルモールド
- 最適な用途: 高温、高圧
- 準備完了まで: 3 週間
- 適している用途: 数百の部品
私たちの カスタムカーボンファイバー 部品はタイプ #1 または #2 で始まります。
ステップ3: ベースモールドを印刷する
3D プリントされた金型を使用する場合:
- 3DプリンターにPVAフィラメントを装填する
- 滑らかな仕上がりのために、印刷設定を0.1mmのレイヤーに設定します。
- 最良の結果を得るには215°Cで印刷してください
- 取り扱う前に完全に冷ましてください
警告: 印刷物に凹凸や穴がないか確認してください。これらは最終パーツに現れます。
ステップ4: 型の表面を準備する
次に、カーボン用の型を準備します。
- 400番の紙やすりで磨く
- アルコールで拭き取る
- 適用する 離型剤 3回
- 20分間乾燥させてください
このステップは 非常に重要! スキップすると、あなたのパートは永久に残ります。
ステップ5: カーボンファイバークロスを切る
カーボンを準備する時間です:
- カーボン用の鋭いハサミを使用してください
- 型より1インチ大きいサイズに切ります
- 1mmの厚さに3層にする
- 使用するまで平らに保管してください
私たちの カーボンファイバー 布にはさまざまな織り方があります。ほとんどの型には綾織りが最適です。
ステップ6:樹脂を混ぜる
樹脂を準備します:
- 樹脂と硬化剤を混ぜる(ブランドの比率を確認してください)
- 3分間ゆっくりかき混ぜる
- 最適な流れを得るには、温度を20~30℃に保ちます。
ホットヒント: 部屋が暑い場合は、混ぜる前に樹脂を冷蔵庫で 30 分間冷やしてください。
ステップ7: カーボンファイバーを敷き詰める
次に型を作ります。
- 型の表面に樹脂を塗る
- 最初のカーボンファイバー層を敷く
- ブラシで押して空気を抜く
- 樹脂をさらに追加
- すべてのレイヤーで繰り返す
素早く、しかし慎重に作業してください。強度を上げるために繊維の方向を交差させてください。
ステップ8:型を真空パックする
このステップにより、型が強くなります。
- 真空バッグに型を入れる
- すべての端をシールする
- 真空ポンプを接続する
- 引張圧力 -0.8 バール
- 漏れがないか確認する
- 最低2時間掃除機をかける
真空により空気と余分な樹脂が押し出され、型がより強くなります。
ステップ9: 硬化させる
型が固まるまで待ちます。
- 室温で24時間放置する
- 強度を高めるには、60°Cで2時間後硬化してください。
- 完全に冷めるまで待ってから取り外してください
重要: このステップを急がないでください。完全な強度を得るには、十分な硬化時間が必要です。
ステップ10: 削除して終了
最後の手順:
- 型をベースからそっとこじ開けます
- 切削工具で余分な部分を切り取る
- エッジを滑らかにする
- 最終離型剤を塗布する
カーボンファイバーの型が完成し、部品を作る準備ができました。
実際の結果: ケーススタディ
当店の実際の結果をご覧ください:
自動車用エアインテーク金型
- 旧方式:金型費用$15,000、所要6週間
- 私たちのやり方:カーボンファイバーの金型は$1,200の費用がかかり、5日かかりました
- 貯蓄: $13,800と5週間の時間
自動車メーカーは設計を5倍速くテストできるようになりました。現在、彼らはすべての新製品に当社の方法を採用しています。 カーボンファイバーカー 部品。
よくある問題と簡単な解決方法
プロでも時々問題が発生することがあります。
問題 | 原因 | すぐに解決する |
---|---|---|
金型内の泡 | レイアップが速すぎる | ゆっくり作業し、掃除機を長く使用する |
型の固着 | 離型剤が足りない | 次回は5回塗ります |
弱点 | 不均一な樹脂 | 樹脂注入法を使用する |
ワーピング | 熱が強すぎる | まず室温で硬化させる |
当社のカーボンファイバー金型が優れている理由
当社の金型は、さまざまな点で金属製の金型よりも優れています。
- 料金: 85%は金属より安い
- スピード: 数週間ではなく数日で準備完了
- 重さ: 70%は金属より軽い
- 熱伝達: より均一な加熱/冷却
- 感じる: 触ると温かいです(従業員はこれを気に入っています!)
多くの カーボンファイバーバイク 部品は現在、当社の金型方法で製造されています。
28年の経験から得た高度なヒント
本当にプロレベルの型を作りたいですか? これらをお試しください:
- 型材料を混ぜる – コスト削減のため、ガラス繊維の第1層を追加
- モジュラー型を作る – 大きな部品を組み立てる際にフィットするセクションを構築する
- ジェルコートを使用する – 超滑らかな仕上がりのために特別なコーティングを施します
- 加熱要素を追加する – 硬化を制御するための埋め込みワイヤー
- マスターパターンを作成する – 完璧な型を1つ作って、たくさんのコピーを作る
カーボンファイバーのパートナーとして当社を選ぶ理由
私たちは 28 年以上のノウハウをお客様のプロジェクトに提供します。
- カスタムソリューション あらゆる部分
- 迅速な対応 回
- 品質管理 あらゆる段階で
- コスト削減 あなたに渡されました
- ワンストップショップ あらゆる炭素ニーズに対応
今すぐ始めましょう
カーボンファイバー型を試す準備はできましたか? 方法は次のとおりです:
- 部品設計をお送りください
- 最適な金型タイプをご提案いたします
- 24時間以内に無料見積もりをゲット
- 承認してすぐに開始します
- 数日で金型を受け取る
旧式の金型に時間とお金を無駄にするのはやめましょう。当社のカーボンファイバーの専門知識を信頼する多くの企業に加わってください。
今すぐ +86-136 2619 1009 までお電話いただくか、[email protected] までメールでお問い合わせください。