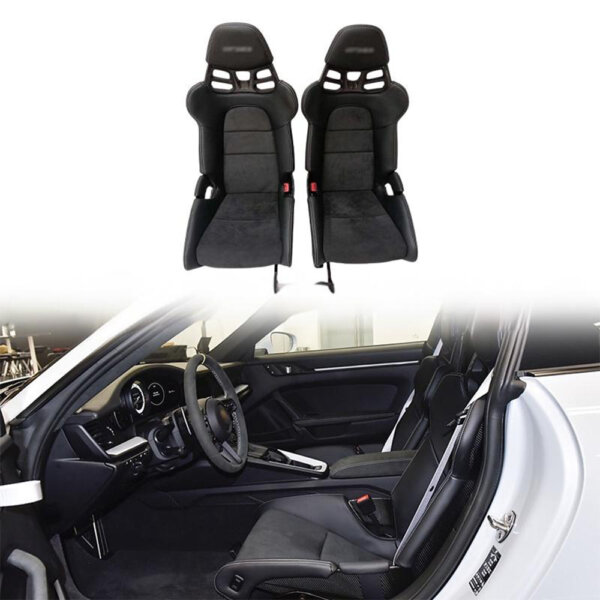
Fibre de carbone sèche ou carbone humide : Guide de comparaison ultime
Introduction
Les polymères renforcés de fibres de carbone (PRFC) sont des matériaux composites connus pour leur rapport poids/résistance, leur rigidité et leur durabilité exceptionnels. Ces propriétés les rendent indispensables dans des secteurs tels que l'aérospatiale, l'automobile et les équipements sportifs de haute performance. Lorsque l'on parle de "fibre de carbone", il s'agit généralement de feuilles de fibre de carbone liées à une résine polymère, généralement de l'époxy.
Cependant, la confusion règne souvent autour des termes "Fibre de carbone humide et "fibre de carbone sèche". Une idée fausse très répandue est que ces étiquettes décrivent la finition de la surface - en supposant que "humide" signifie brillant et "sec" signifie mat. En réalité, ces termes font référence à deux processus de fabrication distincts utilisé pour laminer la fibre de carbone avec de la résine.
Cet article clarifie les différences entre la fibre de carbone humide et la fibre de carbone sèche, compare leur qualité et leurs performances, et explore les considérations pratiques pour les acheteurs. Que vous soyez ingénieur, amateur ou simplement curieux des matériaux avancés, la compréhension de ces distinctions vous aidera à prendre des décisions éclairées.
Procédés de fabrication
Fibre de carbone humide
Le méthode de stratification par voie humide est l'approche la plus traditionnelle pour produire des pièces en fibre de carbone. Voici comment cela fonctionne :
- Application manuelle de la résine: La résine époxy liquide est appliquée au pinceau ou pulvérisée sur des feuilles de fibre de carbone sèches placées dans un moule.
- Superposition: Plusieurs feuilles peuvent être empilées pour obtenir l'épaisseur souhaitée.
- Durcissement: La résine durcit à température ambiante ou sous l'effet d'une légère chaleur, liant les fibres en une structure solide.
Outils utilisés: Brosses, rouleaux ou pistolets pour l'application de la résine ; mise sous vide (optionnelle) pour réduire les bulles d'air.
Avantages:
- Faibles coûts d'équipement (pas d'autoclave nécessaire).
- Flexibilité pour les projets personnalisés ou uniques.
Inconvénients:
- Distribution irrégulière de la résine, entraînant des points faibles potentiels.
- Risque plus élevé de défauts tels que des poches d'air ou un durcissement inégal.
Fibre de carbone sèche
Fibre de carbone sèche, ou fibre de carbone pré-imprégnéeutilise un processus de fabrication plus avancé :
- Tissu pré-imprégné: Les feuilles de fibre de carbone sont pré-revêtues d'une quantité précise de résine non durcie dans des conditions contrôlées en usine.
- Lay-up: Les feuilles pré-imprégnées sont placées dans un moule et recouvertes d'un sac sous vide.
- Durcissement: L'assemblage est chauffé dans un autoclave (ou four) sous haute pression, ce qui garantit un écoulement uniforme de la résine et un collage optimal.
Principaux avantages:
- Cohérence supérieure dans la distribution de la résine et l'alignement des fibres.
- Rapport résistance/poids plus élevé et moins de défauts.
Limites:
- Nécessite un équipement coûteux (autoclaves).
- Moins accessible pour les projets à petite échelle ou les projets de bricolage.
Principales différences en termes de qualité et de performance
Lorsqu'il s'agit de choisir entre la fibre de carbone humide et la fibre de carbone sèche, il est essentiel de comprendre leurs différences structurelles et mécaniques pour sélectionner le bon matériau pour votre application.
Cohérence et intégrité structurelle
- Fibre de carbone sèche:
- La distribution de la résine contrôlée en usine garantit saturation uniforme des fibres, en éliminant les points faibles.
- La polymérisation en autoclave s'applique pression et chaleur uniformesLe système d'étanchéité est conçu de manière à minimiser les vides et les zones riches en résine.
- Fibre de carbone humide:
- Risques liés à l'application manuelle de résine revêtement irrégulierce qui entraîne une résistance inégale.
- Vulnérable aux bulles d'air, points secs ou accumulation de résine en excèsce qui peut compromettre la durabilité.
Rapport résistance/poids
- CF sec excelle dans les applications à haute performance grâce à :
- Rapport fibre/résine optimisé (typiquement 30-40% résine en poids).
- Plus haut rigidité et résistance à la traction que la FC humide.
- CF humide peut sacrifier une partie de la force au profit de la souplesse :
- La teneur en résine est souvent supérieure à 40%, ce qui ajoute un poids inutile.
- Convient pour parties non structurelles lorsque la résistance absolue n'est pas essentielle.
Taux de défectuosité et longévité
- CF sec:
- Porosité quasi nulle (<1%) grâce au traitement en autoclave.
- Résistant aux délaminage et des microfissures au fil du temps.
- CF humide:
- Sujet à vides (porosité 5-10%) sans mise sous vide.
- Risque plus élevé de Dégradation par les UV si la résine n'est pas complètement durcie.
Considérations pratiques pour les acheteurs
Comparaison des coûts
Facteur | Fibre de carbone sèche | Fibre de carbone humide |
---|---|---|
Coût initial | Élevé ($100-$500/kg pour le pré-imprégné) | Faible ($20-$100/kg pour les matériaux) |
Matériel nécessaire | Autoclave ($50k–$1M+) | Outils de base (pinceau, moule) |
Intensité du travail | Faible (le pré-imprégné est pré-fabriqué) | Haut (compétences manuelles en matière de layup) |
Compromis:
- CF secs coût plus élevé se justifie pour l'aérospatiale ou la course automobile où l'échec n'est pas envisageable.
- La FC humide est économique pour les prototypes ou les pièces décoratives.
Applications
- La FC sèche domine en:
- Aérospatial: Fuselage du Boeing 787 Dreamliner.
- Supercars: Châssis McLaren Monocage.
- Sports d'élite: Composants de Formule 1, cadres de bicyclettes haut de gamme.
- CF humide Convient:
- Automobile sur mesure: Kits de carrosserie, garnitures intérieures.
- Projets de bricolage: Cadres de drones, corps de guitares.
- Réparations: Rattrapage des parties endommagées des FC (par exemple, les coques de bateaux).
Durabilité et entretien
- Résistance à l'environnement:
- La matrice de résine serrée du Dry CF résiste mieux à l'usure et à la corrosion. l'humidité, les produits chimiques et les UV.
- La FC humide peut nécessiter revêtements protecteurs pour une utilisation en extérieur.
- Réparabilité:
- La FC humide est plus facile à correctif avec de la résine coulée à la main.
- Les réparations de la CF sèche nécessitent souvent réticulation professionnelle en autoclave.
Démystifier les mythes courants sur la fibre de carbone
La fibre de carbone est entourée d'idées fausses, notamment en ce qui concerne les méthodes de fabrication par voie humide et par voie sèche. Clarifions deux grands mythes :
Mythe 1 : "La fibre de carbone humide est brillante, la fibre de carbone sèche est mate".
- Réalité: Les termes "humide" et "sec" se réfèrent à uniquement au processus de fabricationet non l'état de surface.
- Options de finition: Les deux types peuvent atteindre brillant, mat ou satiné les finitions en fonction de :
- Résine de finition (par exemple, un vernis résistant aux UV pour la brillance).
- Additifs (par exemple, les agents de matage mélangés à l'époxy).
- Exemple: Un capot en fibre de carbone sec peut être poli pour obtenir une finition miroir, tandis que la fibre de carbone humide peut être laissée mate pour un aspect furtif.
Mythe 2 : "La fibre de carbone sèche est toujours meilleure".
- Réalité: Dry CF surpasse les performances en applications soumises à de fortes contraintesmais la FC humide présente des avantages :
- Rapport coût-efficacité: Idéal pour prototypes uniques ou des parties non porteuses (par exemple, des panneaux décoratifs).
- Flexibilité: Plus facile à former à la main des formes complexes sans contraintes d'autoclave.
- Réparabilité: La stratification par voie humide est plus simple pour réparations sur le terrain (par exemple, réparer un carénage de moto fissuré).
- Quand choisir la FC humide:
- Projets à budget limité.
- Production en petites séries lorsque l'outillage pour la CF sèche n'est pas pratique.
Facteurs environnementaux et bricolage
Durabilité de la production de fibres de carbone
Facteur | Fibre de carbone sèche | Fibre de carbone humide |
---|---|---|
Consommation d'énergie | Élevé (l'autoclave consomme ~50 kWh par pièce) | Faible (durcissement à température ambiante) |
Déchets de résine | Minimal (quantités précises de pré-imprégnés) | L'excès de résine est souvent jeté |
Recyclabilité | Défi (époxy thermodurcissable) | Mêmes limites, mais émergence de bio-résines |
Des avancées respectueuses de l'environnement:
- CF recyclé: Certains fabricants déchiquettent les fibres de rebut pour les réutiliser dans des pièces non structurelles.
- Résines biosourcées: Des époxydes expérimentaux dérivés de plantes réduisent la dépendance à l'égard des produits pétrochimiques.
Faisabilité du bricolage
- Fibre de carbone humide:
- Débutant: Nécessite uniquement outils de base (pinceaux, moules et résine).
- Projets populaires: Garniture de voiture personnalisée, cadre de drone ou armure de cosplay.
- Tutoriels: Il existe de nombreux guides en ligne sur la stratification humide à petite échelle.
- Fibre de carbone sèche:
- Obstacles: Les autoclaves sont coût prohibitif pour les amateurs ($50k+).
- Solutions de rechange: Quelques utilisations préimprégnés étuvés (limité à de petites pièces).
- Laboratoires communautaires: Les espaces de création partagés offrent parfois un accès à l'autoclave.
Note de sécurité:
- Toujours travailler dans un zone bien ventilée-Les fumées d'époxy sont toxiques.
- Porter gants et lunettes pour prévenir l'irritation de la peau due à la résine non polymérisée.
Applications industrielles : Où la fibre de carbone sèche et humide brille
Les propriétés uniques de la fibre de carbone l'ont rendue indispensable dans les industries de haute performance. Voici comment les fibres de carbone humides et sèches sont utilisées dans des applications réelles :
Automobile : Précision et praticité
La fibre de carbone sèche domine les performances haut de gamme
- Composants structurels: Utilisé dans châssis monocoque (par exemple, McLaren Senna, Ferrari SF90) pour une rigidité maximale et des économies de poids.
- Pièces critiques: Les arbres de transmission, les bras de suspension et les composants de freinage bénéficient de la constance de la CF sèche.
- Courses: Les équipes de Formule 1 utilisent des pré-imprégnés polymérisés en autoclave pour les composants aérodynamiques.
Fibre de carbone humide pour la personnalisation et la rentabilité
- Kits carrosserie: Les capots, spoilers et ailes du marché secondaire sont souvent réalisés par stratification humide pour des raisons de coût.
- Garniture intérieure: Panneaux décoratifs du tableau de bord ou accents de porte où une résistance extrême n'est pas requise.
- Restaurations: Réparations de voitures classiques où l'esthétique de l'époque est plus importante que la répartition parfaite de la résine.
Étude de cas : Mercedes-AMG
- Dry CF : des éléments structurels tels que le Tube de couple de l'AMG GT.
- CF humide : en option ensembles extérieurs en fibre de carbone pour l'attrait visuel.
Aérospatiale : Là où chaque gramme compte
- La fibre de carbone sèche est la norme
- Structures d'aéronefs: Les fuselages du Boeing 787 et de l'Airbus A350 utilisent des pré-imprégnés polymérisés en autoclave pour la résistance à la fatigue.
- Vaisseau spatial: Les supports du bouclier thermique de SpaceX Dragon tirent parti de la stabilité thermique du CF sec.
- Rôles de niche de la fibre de carbone humide
- Prototypage: Des maquettes rapides et peu coûteuses pour tester l'aérodynamisme.
- Pièces non critiques: Séparateurs de cabine ou bacs de rangement lorsque le poids n'est pas une préoccupation majeure.
Conclusion : Choisir la bonne fibre de carbone pour vos besoins
Récapitulation des principales différences
Facteur | Fibre de carbone sèche | Fibre de carbone humide |
---|---|---|
Idéal pour | Applications critiques en termes de performances | Projets personnalisés et sensibles aux coûts |
Coût | Élevé (équipement + matériel) | Faible (peu d'outils nécessaires) |
Niveau de compétence | Expertise industrielle nécessaire | Convivialité du bricolage |
Tendances futures de la technologie des fibres de carbone
- Pose automatisée: Robots pour la stratification humide afin de réduire l'erreur humaine (par exemple, la production de CFRP de BMW).
- Préimprégnés hors autoclave (OoA): De nouvelles résines qui durcissent dans des fours, réduisant ainsi la barrière à l'entrée de la CF sèche.
- Solutions durables:
- Thermoplastiques recyclables: Alternatives à l'époxy traditionnel (par exemple, la résine Elium d'Arkema).
- Recyclage en circuit fermé: Des entreprises comme Toray Industries récupèrent le CF des avions en fin de vie.
Recommandation finale
- Choisissez la fibre de carbone sèche si: Vous avez besoin performances maximales et disposent d'un budget pour le traitement en autoclave.
- Choisissez la fibre de carbone humide si: Vous établissez des priorités la flexibilité, l'accessibilité financière ou la personnalisation par le bricoleur.
La fibre de carbone continue d'évoluer, comblant le fossé entre l'ingénierie de haute technologie et l'artisanat accessible. Que vous construisiez une voiture de course ou un cadre de vélo personnalisé, la connaissance de ces options vous permettra de tirer le meilleur parti de ce matériau révolutionnaire.
Vous avez un projet en tête ? Faites-nous part de vos questions ci-dessous - nous serons heureux de vous aider !