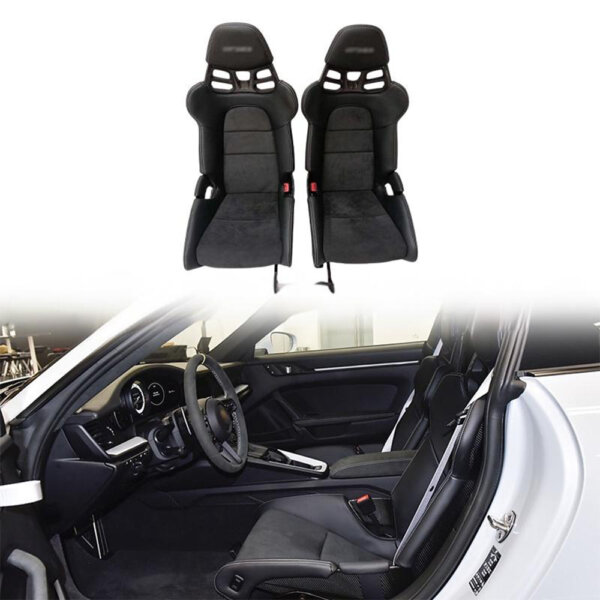
Droge koolstofvezel vs natte koolstof: ultieme vergelijkingsgids
Inleiding
Koolstofvezelversterkte polymeren (CFRP) zijn composietmaterialen die bekend staan om hun uitzonderlijke sterkte-gewichtsverhouding, stijfheid en duurzaamheid. Deze eigenschappen maken ze onmisbaar in industrieën zoals lucht- en ruimtevaart, auto's en hoogwaardige sportuitrustingen. Wanneer mensen verwijzen naar "koolstofvezel", hebben ze het meestal over CFRP-koolstofvezelplaten gebonden met een polymeerhars, meestal epoxy.
Er ontstaat echter vaak verwarring over de termen "natte koolstofvezel" En "droge koolstofvezel." Een veel voorkomende misvatting is dat deze labels de afwerking van het oppervlak beschrijven, waarbij wordt aangenomen dat "nat" glanzend betekent en "droog" mat. In werkelijkheid verwijzen de termen naar twee verschillende productieprocessen gebruikt om koolstofvezel te lamineren met hars.
Dit artikel verduidelijkt de verschillen tussen natte en droge koolstofvezel, vergelijkt hun kwaliteit en prestaties en onderzoekt praktische overwegingen voor kopers. Of je nu een ingenieur, hobbyist of gewoon nieuwsgierig bent naar geavanceerde materialen, als je dit onderscheid begrijpt, kun je weloverwogen beslissingen nemen.
Productieprocessen
Natte koolstofvezel
De natte lay-up methode is de meer traditionele benadering voor het produceren van koolstofvezelonderdelen. Dit is hoe het werkt:
- Handmatig hars aanbrengen: Vloeibare epoxyhars wordt geborsteld of gespoten op droge koolstofvezelplaten die in een mal zijn geplaatst.
- Lagen: Meerdere vellen kunnen gestapeld worden om de gewenste dikte te verkrijgen.
- Uitharden: De hars hardt uit bij kamertemperatuur of met milde hitte, waardoor de vezels in een vaste structuur worden gebonden.
Gebruikt gereedschap: Kwasten, rollen of spuitpistolen voor het aanbrengen van hars; vacuümzakken (optioneel) om luchtbellen te verminderen.
Voordelen:
- Lage uitrustingskosten (geen autoclaaf nodig).
- Flexibiliteit voor aangepaste of eenmalige projecten.
Nadelen:
- Inconsistente harsdistributie, wat leidt tot potentiële zwakke plekken.
- Hoger risico op defecten zoals luchtzakken of ongelijkmatige uitharding.
Droge koolstofvezel
Droge koolstofvezel, of prepreg (voorgeïmpregneerde) koolstofvezelmaakt gebruik van een geavanceerder productieproces:
- Prepreg stof: Koolstofvezelplaten worden vooraf gecoat met een precieze hoeveelheid niet-uitgeharde hars onder fabrieksgecontroleerde omstandigheden.
- Opmaak: De prepreg vellen worden in een mal gelegd en afgedekt met een vacuüm gesealde zak.
- Uitharden: De assemblage wordt verwarmd in een autoclaaf (of oven) onder hoge druk, voor een gelijkmatige harsstroom en optimale hechting.
Belangrijkste voordelen:
- Superieure consistentie in harsverdeling en vezeluitlijning.
- Hogere sterkte-gewichtsverhouding en minder defecten.
Beperkingen:
- Vereist dure apparatuur (autoclaven).
- Minder toegankelijk voor kleinschalige of doe-het-zelfprojecten.
Belangrijkste verschillen in kwaliteit en prestaties
Bij de keuze tussen natte en droge koolstofvezels is inzicht in de structurele en mechanische verschillen cruciaal om het juiste materiaal voor je toepassing te kiezen.
Consistentie en structurele integriteit
- Droge koolstofvezel:
- In de fabriek gecontroleerde harsdistributie garandeert uniforme verzadiging van vezels, waardoor zwakke plekken worden geëlimineerd.
- Autoclaaf uitharding is van toepassing gelijkmatige druk en warmteen minimaliseert holtes of harsrijke gebieden.
- Natte koolstofvezel:
- Risico's van handmatig harsen inconsistente coatingwat leidt tot ongelijke sterkte.
- Kwetsbaar voor luchtbellen, droge plekken of overtollig hars dat zich samenvoegtwat de duurzaamheid in gevaar kan brengen.
Verhouding sterkte/gewicht
- Droog CF blinkt uit in toepassingen met hoge prestaties dankzij:
- Geoptimaliseerde vezel/hars-verhouding (meestal 30-40% hars in gewicht).
- Hoger stijfheid en treksterkte dan natte CF.
- Nat CF kan wat kracht opofferen voor flexibiliteit:
- Het harsgehalte is vaak hoger dan 40%, waardoor onnodig gewicht wordt toegevoegd.
- Geschikt voor niet-structurele onderdelen waar absolute kracht niet kritisch is.
Defectenpercentages en levensduur
- Droog CF:
- Bijna-nul porositeit (<1%) door autoclaafverwerking.
- Bestand tegen delaminatie en microscheurtjes na verloop van tijd.
- Nat CF:
- Gevoelig voor holtes (5-10% porositeit) zonder vacuümzakken.
- Hoger risico op UV-degradatie als hars niet volledig is uitgehard.
Praktische overwegingen voor kopers
Kostenvergelijking
Factor | Droge koolstofvezel | Natte koolstofvezel |
---|---|---|
Voorafgaande kosten | Hoog ($100-$500/kg voor prepreg) | Laag ($20-$100/kg voor materialen) |
Benodigde apparatuur | Autoclave ($50k–$1M+) | Basisgereedschap (kwast, mal) |
Arbeidsintensiteit | Laag (prepreg is kant-en-klaar) | Hoog (handmatige lay-up vaardigheden) |
Afwegingen:
- Droge CF's hogere kostprijs is gerechtvaardigd voor lucht- en ruimtevaart of racen waar falen geen optie is.
- Natte CF is budgetvriendelijk voor prototypes of decoratieve onderdelen.
Toepassingen
- Droge CF domineert in:
- Lucht- en ruimtevaart: Boeing 787 Dreamliner romp.
- Superauto's: McLaren Monocage chassis.
- Elite Sporten: Formule 1-onderdelen, hoogwaardige fietsframes.
- Natte CF past:
- Aangepaste auto: Carrosseriekits, interieurbekleding.
- Doe-het-zelf projecten: Frames voor drone's, body's voor gitaren.
- Reparaties: Repareren van beschadigde CF-onderdelen (bijv. scheepsrompen).
Duurzaamheid en onderhoud
- Milieubestendigheid:
- De dichte harsmatrix van Dry CF is beter bestand tegen vocht, chemicaliën en UV.
- Natte CF kan het volgende vereisen beschermende coatings voor gebruik buitenshuis.
- Repareerbaarheid:
- Nat CF is gemakkelijker te patch met handgemaakte hars.
- Voor droge CF-reparaties is vaak het volgende nodig professionele heruitharding in autoclaaf.
Veelvoorkomende mythes over koolstofvezel ontkrachten
Koolstofvezel wordt omgeven door misvattingen, vooral over natte en droge productiemethoden. Laten we twee grote mythes ophelderen:
Mythe 1: "Natte koolstofvezel is glanzend, droge koolstofvezel is mat".
- Werkelijkheid: De termen "nat" en "droog" verwijzen naar alleen voor het productieprocesniet de afwerking van het oppervlak.
- Afwerkingsopties: Beide types kunnen het volgende bereiken glanzend, mat of satijn afwerkingen afhankelijk van:
- Topcoat hars (bijv. UV-bestendige blanke lak voor glans).
- Toevoegingen (bijv. matteringsmiddelen gemengd in epoxy).
- Voorbeeld: Een droge koolstofvezel kap kan worden gepolijst tot een spiegelende afwerking, terwijl natte koolstofvezel mat kan worden gelaten voor een stealth look.
Mythe 2: "Droge koolstofvezel is altijd beter".
- Werkelijkheid: Dry CF presteert beter in toepassingen met hoge belastingmaar natte CF heeft voordelen:
- Kosteneffectiviteit: Ideaal voor eenmalige prototypes of niet-dragende delen (bijv. decoratieve panelen).
- Flexibiliteit: Gemakkelijker om complexe vormen met de hand vormen zonder autoclaafbeperkingen.
- Repareerbaarheid: Nat lay-up is eenvoudiger voor veldreparaties (bijvoorbeeld het repareren van een gebarsten motorkap).
- Wanneer voor Wet CF kiezen?:
- Projecten met een beperkt budget.
- Productie in kleine series waarbij gereedschap voor droge CF onpraktisch is.
Milieu- en doe-het-zelffactoren
Duurzaamheid van de productie van koolstofvezels
Factor | Droge koolstofvezel | Natte koolstofvezel |
---|---|---|
Energieverbruik | Hoog (autoclaaf verbruikt ~50 kWh per onderdeel) | Laag (hardt uit bij kamertemperatuur) |
Harsafval | Minimaal (precieze prepreg hoeveelheden) | Overtollig hars wordt vaak weggegooid |
Recycleerbaarheid | Uitdagend (thermohardende epoxies) | Dezelfde beperkingen, maar sommige bioharsen zijn in opkomst |
Milieuvriendelijke vooruitgang:
- Gerecycled CF: Sommige fabrikanten versnipperen afvalvezels voor hergebruik in niet-structurele onderdelen.
- Bio-gebaseerde harsen: Experimentele epoxies op basis van planten verminderen de afhankelijkheid van petrochemische stoffen.
Doe-het-zelf haalbaarheid
- Natte koolstofvezel:
- Beginnersvriendelijk: Vereist alleen basisgereedschappen (penselen, mallen en hars).
- Populaire projecten: Aangepaste autoafwerking, droneframes of cosplaypantser.
- Lesmateriaal: Er zijn online gidsen in overvloed voor kleinschalige wet lay-up.
- Droge koolstofvezel:
- Belemmeringen: Autoclaven zijn onbetaalbaar voor hobbyisten ($50k+).
- Workarounds: Enig gebruik ovenharde prepregs (beperkt tot kleine onderdelen).
- Laboratoria: Gedeelde makerspaces bieden soms toegang tot autoclaven.
Veiligheidsaanwijzing:
- Werk altijd in een goed geventileerde ruimte-epoxydampen zijn giftig.
- Draag handschoenen en veiligheidsbril om huidirritatie door niet-uitgeharde hars te voorkomen.
Industriële toepassingen: Waar natte en droge koolstofvezels schitteren
De unieke eigenschappen van koolstofvezel hebben het onmisbaar gemaakt in high-performance industrieën. Dit is hoe natte en droge koolstofvezels worden gebruikt in echte toepassingen:
Automobiel: Precisie vs. Praktisch
Droge koolstofvezel domineert hoogwaardige prestaties
- Structurele onderdelen: Gebruikt in monocoque chassis (bijv. McLaren Senna, Ferrari SF90) voor maximale stijfheid en gewichtsbesparing.
- Kritieke onderdelen: Aandrijfassen, ophangingsarmen en remonderdelen profiteren van de consistentie van droge CF.
- Racen: Formule 1-teams vertrouwen op autoclaafgeharde prepreg voor aerodynamische onderdelen.
Natte koolstofvezel voor maatwerk en kostenefficiëntie
- Bodykits: Bij aftermarket motorkappen, spoilers en spatborden wordt vaak gebruik gemaakt van wet lay-up voor de betaalbaarheid.
- Interieurbekleding: Decoratieve dashboards of deuraccenten waar geen extreme sterkte vereist is.
- Restauraties: Klassieke autoreparaties waarbij de vintage esthetiek belangrijker is dan een perfecte harsverdeling.
Casestudie: Mercedes-AMG
- Droog CF: Structurele elementen zoals de De koppelbuis van de AMG GT.
- Natte CF: Optioneel koolstofvezel exterieurpakketten voor visuele aantrekkingskracht.
Ruimtevaart: Waar elke gram telt
- Droge koolstofvezel is de standaard
- Vliegtuigstructuren: Boeing 787 en Airbus A350 rompen gebruiken autoclaaf uitgeharde prepreg voor weerstand tegen vermoeiing.
- Ruimtevaartuig: Het hitteschild van SpaceX Dragon maakt gebruik van de thermische stabiliteit van droog CF.
- Niche-rollen van nat koolstofvezel
- Prototype maken: Snelle, goedkope mockups voor het testen van aerodynamica.
- Niet-kritieke onderdelen: Kajuitverdelers of opbergbakken waarbij gewicht niet van primair belang is.
Conclusie: De juiste koolstofvezel voor uw behoeften kiezen
Overzicht van belangrijkste verschillen
Factor | Droge koolstofvezel | Natte koolstofvezel |
---|---|---|
Beste voor | Prestatie-kritische toepassingen | Aangepaste, kostengevoelige projecten |
Kosten | Hoog (uitrusting + materialen) | Laag (minimaal gereedschap nodig) |
Vaardigheidsniveau | Industriële expertise nodig | Doe-het-zelf-vriendelijk |
Toekomstige trends in koolstofvezeltechnologie
- Geautomatiseerde opmaak: Robots voor wet lay-up om menselijke fouten te verminderen (bijv. BMW's CFRP productie).
- Prepregs buiten de autoclaaf (OoA): Nieuwe harsen die uitharden in ovens, waardoor de drempel voor droge CF lager wordt.
- Duurzame oplossingen:
- Recyclebare thermoplasten: Alternatieven voor traditionele epoxy (bijv. Elium hars van Arkema).
- Kringloopsluiting: Bedrijven zoals Toray Industries die CF terugwinnen uit afgedankte vliegtuigen.
Definitieve aanbeveling
- Kies voor droge koolstofvezel als: U moet maximale prestatie en het budget hebben voor verwerking in een autoclaaf.
- Kies Natte koolstofvezel als: Je stelt prioriteiten flexibiliteit, betaalbaarheid of doe-het-zelf-aanpassing.
Koolstofvezel blijft zich ontwikkelen en slaat een brug tussen high-tech techniek en toegankelijk vakmanschap. Of je nu een raceauto bouwt of een fietsframe op maat, als je deze opties begrijpt, haal je het beste uit dit revolutionaire materiaal.
Heb je een project in gedachten? Deel je vragen hieronder - we helpen je graag!