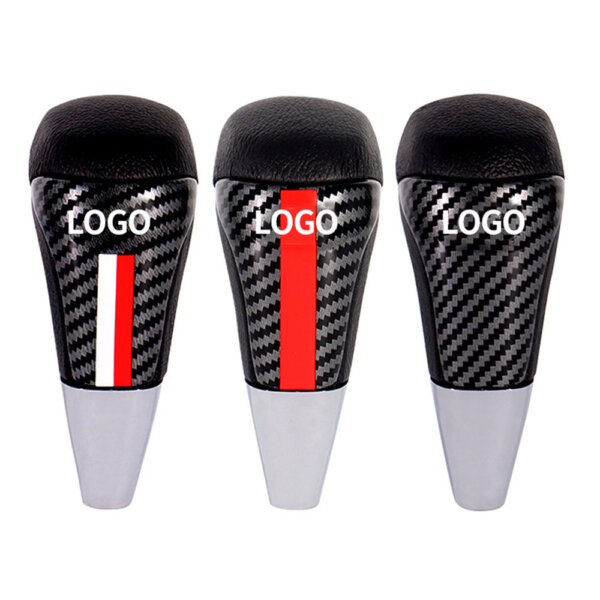
How to Make Forged Carbon Fiber: Easy Way to Get Strong Parts
What is Forged Carbon Fiber?
Forged carbon fiber is a cool composite material. It looks like black marble. It is strong. It is light. Many big car makers use it now.
Do you want to know how to make it? We will tell you all about it!
Our team at SCOMP Carbon Fiber is known for its high-quality forged composite products. We has made forged carbon for 28+ years. We know all the tricks!
The Big Problem with Carbon Fiber
Carbon fiber parts look good. They are strong. But they have three big problems:
- They cost too much money
- They take too much time to make
- They need special skills
This makes many people sad. You want cool carbon parts but can’t get them.
Think about it:
- You need perfect weave patterns
- You need exact cutting
- You need perfect molding
- You waste a lot of material
This gets worse when you need many parts fast. What do you do? The deadline gets closer. The costs go up.
Why Forged Carbon Fiber is the Answer
Forged carbon fiber fixes these problems!
Instead of perfect weaves, you use small cut pieces. Instead of perfect layup, you mix them with resin. Then you press it into shape!
This means:
- Less waste – use scraps and leftover pieces
- Faster making – no need for perfect layup
- Cool marble look – each part looks unique
- Strong parts – 90-95% as strong as regular carbon fiber
Our customers at SCOMP Carbon Fiber love this! We make forged carbon fiber Lamborghini parts that look just like factory parts!
How to Make Forged Carbon Fiber: Step by Step
Let’s make forged carbon fiber the easy way! Follow these steps:
Step 1: Get Your Materials Ready
You need:
- Carbon fiber (can be scraps or waste pieces)
- Epoxy resin (must flow well)
- Mold (can be 3D printed for small parts)
- Release agent (stops sticking)
- Cutting tools (scissors work fine)
- Mixing cups and sticks
- Press (or weights for DIY using fiberglass)
Don’t worry about perfect carbon. Scraps work great! This saves money.
Step 2: Cut Carbon Fiber into Small Pieces
Take your carbon fiber and cut it into small bits:
- Cut about ½ inch pieces (1-2 cm)
- Make them random sizes for the best look
- Use scissors or shears
- Don’t make them too big or too small
The small size helps the pieces flow better in the mold. This makes the cool marble look that our custom carbon fiber customers love!
Step 3: Mix with Resin
Now mix the carbon bits with resin:
- Use a ratio of 60% carbon to 40% resin by weight
- Mix very well until all carbon is wet
- Work fast before the prepreg resin starts to harden
- Add black color to the resin if you want darker parts
This mix is the key to good forged carbon. Too much resin makes weak parts. Too little makes dry spots.
Step 4: Put in Mold and Press
Next, put the mix in your mold:
- Spray release agent on mold first
- Overfill the mold a little bit
- Close the mold top
- Press with 5-10 MPa pressure
The pressure from compression molding makes the resin flow through all the carbon pieces. This makes the part strong.
For DIY, you can use:
- Car jack and plates
- Strong clamps
- Weights (for flat parts)
Step 5: Heat and Cure
Now you need to make the resin hard:
- Heat to 120-180°C (250-350°F)
- Keep pressure on while heating
- Wait 1-4 hours for full cure
- Let cool down slowly
For home DIY:
- Use a kitchen oven (if safe for this)
- Use heat lamps
- Some resins cure at room temp (takes longer)
Step 6: Take Out and Finish
Last steps:
- Take part out of mold carefully
- Trim extra bits with sand paper
- Polish with fine sand paper (3600 to 6000 grit)
- Add clear coat if you want shine
Now you have a cool forged carbon part made from chopped carbon fiber!
Forged Carbon Fiber vs. Regular Carbon Fiber
Let’s see how they compare:
Type | Looks | Cost | Speed to Make | Strength | Skill Needed |
---|---|---|---|---|---|
Regular Carbon | Weave pattern | $100-150/kg | Slow (days) | Very strong | High |
Forged Carbon | Marble pattern | $50-80/kg | Fast (hours) | Strong (90-95%) | Medium |
DIY Forged | Rough marble | $20-50/kg | Medium (day) | Good (80-90%) | Low |
As you can see, forged carbon wins on cost and speed! That’s why our carbon fiber car customers love it.
Real Uses for Forged Carbon Fiber
People use forged carbon fiber and chopped carbon for many cool things:
Car Parts
- Dash panels
- Shifter knobs
- Spoilers
- Interior trim
Our forged carbon fiber kit for Rolls Royce shows how luxury cars use this material!
Motorcycle Parts
- Fairings
- Gas tank covers
- Fenders
Check our carbon fiber motorcycle page for more ideas!
Home Items
- Cups and mugs
- Ashtrays
- Desk items
- Phone cases
Fashion
- Watch cases
- Rings
- Wallets
- Eyewear
New Ways to Make Forged Carbon Better
Science is making forged carbon even better:
Save Energy with New Heat Methods
A team at University of Limerick made a new way to heat carbon fiber. Their CARBOWAVE project uses microwaves instead of big ovens. This uses 70% less energy!
Use Plants Instead of Oil
Most carbon fiber comes from oil. But now we can use lignin from wood waste to make carbon fiber! The University of Manchester proved this works. This means carbon fiber can be more earth-friendly.
Reuse Carbon Fiber Waste
By 2025, the plan is to reuse 30% of carbon fiber waste. This means less trash and lower costs for everyone.
Common Problems and How to Fix Them
Even experts have troubles sometimes. Here are common problems and fixes:
Problem: Dry Spots
- Fix: Add more resin or mix better
- Fix: Press harder in the mold
Problem: Bubbles
- Fix: Mix more slowly to trap less air
- Fix: Use vacuum if possible before molding
Problem: Sticking to Mold
- Fix: Use more release agent
- Fix: Polish mold surface better
Problem: Not Strong Enough
- Fix: Check your carbon-to-resin ratio
- Fix: Make sure it cures fully with proper heat
Why Choose Our Carbon Fiber as Your Manufacturer
Having problems making perfect carbon fiber parts? We understand!
The problem is clear: Making good carbon fiber parts is hard, costs too much, and takes too long. When you try to make them yourself, you might get poor quality or waste materials.
This gets worse when:
- You need many parts fast
- You need perfect finish every time
- You need to keep costs down
- You need complex shapes
At SCOMP Carbon Fiber, we solve all these problems!
- 28+ years experience making carbon fiber
- OEM/ODM services for your exact needs in composite design
- Both regular and forged carbon options
- Custom designs for any use
- Fast production with perfect quality
- Low minimum orders (just ask us!)
We make everything from Mercedes carbon fiber spoilers to custom parts for any need.
Get Started with Forged Carbon Fiber Today!
Now you know how to make forged carbon fiber! It’s easier than regular carbon fiber, looks cooler with its marble pattern, and saves money too.
You can try making it yourself for small projects. But for perfect parts or big orders, talk to us!
Call us today or visit SCOMP Carbon Fiber to see how we can help you make amazing forged carbon fiber parts!