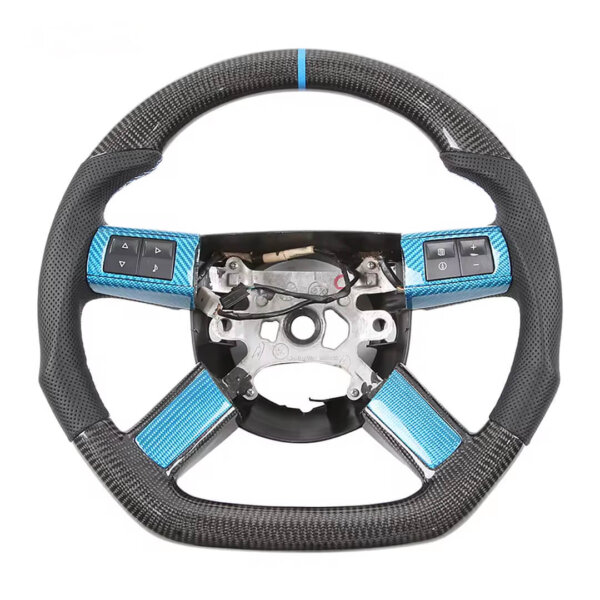
Dry Carbon Fiber vs Wet Carbon: Ultimate Comparison Guide
Introduction
Carbon fiber-reinforced polymers (CFRP) are composite materials known for their exceptional strength-to-weight ratio, stiffness, and durability. These properties make them indispensable in industries like aerospace, automotive, and high-performance sports equipment. When people refer to “carbon fiber,” they’re typically talking about CFRP—carbon fiber sheets bonded with a polymer resin, usually epoxy.
However, confusion often arises around the terms “wet carbon fiber” and “dry carbon fiber.” A common misconception is that these labels describe the surface finish—assuming “wet” means glossy and “dry” means matte. In reality, the terms refer to two distinct manufacturing processes used to laminate carbon fiber with resin.
This article clarifies the differences between wet and dry carbon fiber, compares their quality and performance, and explores practical considerations for buyers. Whether you’re an engineer, hobbyist, or simply curious about advanced materials, understanding these distinctions will help you make informed decisions.
Manufacturing Processes
Wet Carbon Fiber
The wet lay-up method is the more traditional approach to producing carbon fiber parts. Here’s how it works:
- Manual Resin Application: Liquid epoxy resin is brushed or sprayed onto dry carbon fiber sheets placed in a mold.
- Layering: Multiple sheets may be stacked to achieve the desired thickness.
- Curing: The resin hardens at room temperature or with mild heat, bonding the fibers into a solid structure.
Tools Used: Brushes, rollers, or spray guns for resin application; vacuum bagging (optional) to reduce air bubbles.
Pros:
- Low equipment costs (no autoclave needed).
- Flexibility for custom or one-off projects.
Cons:
- Inconsistent resin distribution, leading to potential weak spots.
- Higher risk of defects like air pockets or uneven curing.
Dry Carbon Fiber
Dry carbon fiber, or prepreg (pre-impregnated) carbon fiber, uses a more advanced manufacturing process:
- Prepreg Fabric: Carbon fiber sheets are pre-coated with a precise amount of uncured resin under factory-controlled conditions.
- Layup: The prepreg sheets are placed into a mold and covered with a vacuum-sealed bag.
- Curing: The assembly is heated in an autoclave (or oven) under high pressure, ensuring uniform resin flow and optimal bonding.
Key Advantages:
- Superior consistency in resin distribution and fiber alignment.
- Higher strength-to-weight ratio and fewer defects.
Limitations:
- Requires expensive equipment (autoclaves).
- Less accessible for small-scale or DIY projects.
Key Differences in Quality and Performance
When choosing between wet and dry carbon fiber, understanding their structural and mechanical differences is crucial for selecting the right material for your application.
Consistency & Structural Integrity
- Dry Carbon Fiber:
- Factory-controlled resin distribution ensures uniform saturation of fibers, eliminating weak spots.
- Autoclave curing applies even pressure and heat, minimizing voids or resin-rich areas.
- Wet Carbon Fiber:
- Manual resin application risks inconsistent coating, leading to uneven strength.
- Vulnerable to air bubbles, dry spots, or excess resin pooling, which can compromise durability.
Strength-to-Weight Ratio
- Dry CF excels in high-performance applications due to:
- Optimized fiber-to-resin ratio (typically 30-40% resin by weight).
- Higher stiffness and tensile strength than wet CF.
- Wet CF may sacrifice some strength for flexibility:
- Resin content often exceeds 40%, adding unnecessary weight.
- Suitable for non-structural parts where absolute strength isn’t critical.
Defect Rates & Longevity
- Dry CF:
- Near-zero porosity (<1%) due to autoclave processing.
- Resistant to delamination and micro-cracks over time.
- Wet CF:
- Prone to voids (5-10% porosity) without vacuum bagging.
- Higher risk of UV degradation if resin isn’t fully cured.
Practical Considerations for Buyers
Cost Comparison
Factor | Dry Carbon Fiber | Wet Carbon Fiber |
---|---|---|
Upfront Cost | High ($100–$500/kg for prepreg) | Low ($20–$100/kg for materials) |
Equipment Needed | Autoclave ($50k–$1M+) | Basic tools (brush, mold) |
Labor Intensity | Low (prepreg is pre-engineered) | High (manual layup skills) |
Trade-offs:
- Dry CF’s higher cost is justified for aerospace or racing where failure isn’t an option.
- Wet CF is budget-friendly for prototypes or decorative parts.
Applications
- Dry CF Dominates In:
- Aerospace: Boeing 787 Dreamliner fuselage.
- Supercars: McLaren Monocage chassis.
- Elite Sports: Formula 1 components, premium bicycle frames.
- Wet CF Fits:
- Custom Automotive: Body kits, interior trim.
- DIY Projects: Drone frames, guitar bodies.
- Repairs: Patching damaged CF parts (e.g., boat hulls).
Durability & Maintenance
- Environmental Resistance:
- Dry CF’s tight resin matrix better resists moisture, chemicals, and UV.
- Wet CF may require protective coatings for outdoor use.
- Repairability:
- Wet CF is easier to patch with hand-laid resin.
- Dry CF repairs often require professional autoclave re-curing.
Debunking Common Myths About Carbon Fiber
Carbon fiber is surrounded by misconceptions, especially regarding wet and dry manufacturing methods. Let’s clarify two major myths:
Myth 1: “Wet Carbon Fiber is Glossy, Dry Carbon Fiber is Matte”
- Reality: The terms “wet” and “dry” refer only to the manufacturing process, not the surface finish.
- Finish Options: Both types can achieve glossy, matte, or satin finishes depending on:
- Topcoat resin (e.g., UV-resistant clear coat for shine).
- Additives (e.g., matting agents mixed into epoxy).
- Example: A dry carbon fiber hood can be polished to a mirror finish, while wet carbon fiber can be left matte for a stealth look.
Myth 2: “Dry Carbon Fiber is Always Better”
- Reality: Dry CF outperforms in high-stress applications, but wet CF has advantages:
- Cost-Effectiveness: Ideal for one-off prototypes or non-load-bearing parts (e.g., decorative panels).
- Flexibility: Easier to hand-form complex shapes without autoclave constraints.
- Repairability: Wet lay-up is simpler for field repairs (e.g., fixing a cracked motorcycle fairing).
- When to Choose Wet CF:
- Budget-limited projects.
- Short-run production where tooling for dry CF is impractical.
Environmental and DIY Factors
Sustainability of Carbon Fiber Production
Factor | Dry Carbon Fiber | Wet Carbon Fiber |
---|---|---|
Energy Use | High (autoclave consumes ~50 kWh per part) | Low (cures at room temp) |
Resin Waste | Minimal (precise prepreg amounts) | Excess resin often discarded |
Recyclability | Challenging (thermoset epoxies) | Same limitations, but some bio-resins emerging |
Eco-Friendly Advances:
- Recycled CF: Some manufacturers shred scrap fibers for reuse in non-structural parts.
- Bio-Based Resins: Experimental plant-derived epoxies reduce reliance on petrochemicals.
DIY Feasibility
- Wet Carbon Fiber:
- Beginner-Friendly: Requires only basic tools (brushes, molds, and resin).
- Popular Projects: Custom car trim, drone frames, or cosplay armor.
- Tutorials: Online guides abound for small-scale wet lay-up.
- Dry Carbon Fiber:
- Barriers: Autoclaves are prohibitively expensive for hobbyists ($50k+).
- Workarounds: Some use oven-cured prepregs (limited to small parts).
- Community Labs: Shared maker spaces sometimes offer autoclave access.
Safety Note:
- Always work in a well-ventilated area—epoxy fumes are toxic.
- Wear gloves and goggles to prevent skin irritation from uncured resin.
Industry Applications: Where Wet and Dry Carbon Fiber Shine
Carbon fiber’s unique properties have made it indispensable in high-performance industries. Here’s how wet and dry carbon fiber are used in real-world applications:
Automotive: Precision vs. Practicality
Dry Carbon Fiber Dominates High-End Performance
- Structural Components: Used in monocoque chassis (e.g., McLaren Senna, Ferrari SF90) for maximum rigidity and weight savings.
- Critical Parts: Driveshafts, suspension arms, and brake components benefit from dry CF’s consistency.
- Racing: Formula 1 teams rely on autoclave-cured prepreg for aerodynamic components.
Wet Carbon Fiber for Customization and Cost Efficiency
- Body Kits: Aftermarket hoods, spoilers, and fenders often use wet lay-up for affordability.
- Interior Trim: Decorative dash panels or door accents where extreme strength isn’t required.
- Restorations: Classic car repairs where matching vintage aesthetics matters more than perfect resin distribution.
Case Study: Mercedes-AMG
- Dry CF: Structural elements like the AMG GT’s torque tube.
- Wet CF: Optional carbon fiber exterior packages for visual appeal.
Aerospace: Where Every Gram Counts
- Dry Carbon Fiber is the Standard
- Aircraft Structures: Boeing 787 and Airbus A350 fuselages use autoclave-cured prepreg for fatigue resistance.
- Spacecraft: SpaceX Dragon’s heat shield mounts leverage dry CF’s thermal stability.
- Wet Carbon Fiber’s Niche Roles
- Prototyping: Quick, low-cost mockups for testing aerodynamics.
- Non-Critical Parts: Cabin dividers or storage bins where weight isn’t a primary concern.
Conclusion: Choosing the Right Carbon Fiber for Your Needs
Recap of Key Differences
Factor | Dry Carbon Fiber | Wet Carbon Fiber |
---|---|---|
Best For | Performance-critical applications | Custom, cost-sensitive projects |
Cost | High (equipment + materials) | Low (minimal tools required) |
Skill Level | Industrial expertise needed | DIY-friendly |
Future Trends in Carbon Fiber Technology
- Automated Layup: Robots for wet lay-up to reduce human error (e.g., BMW’s CFRP production).
- Out-of-Autoclave (OoA) Prepregs: New resins that cure in ovens, lowering dry CF’s barrier to entry.
- Sustainable Solutions:
- Recyclable Thermoplastics: Alternatives to traditional epoxy (e.g., Elium resin by Arkema).
- Closed-Loop Recycling: Companies like Toray Industries reclaiming CF from end-of-life aircraft.
Final Recommendation
- Choose Dry Carbon Fiber If: You need maximum performance and have the budget for autoclave processing.
- Choose Wet Carbon Fiber If: You prioritize flexibility, affordability, or DIY customization.
Carbon fiber continues to evolve, bridging the gap between high-tech engineering and accessible craftsmanship. Whether you’re building a race car or a custom bike frame, understanding these options ensures you make the most of this revolutionary material.
Have a project in mind? Share your questions below—we’re happy to help!