
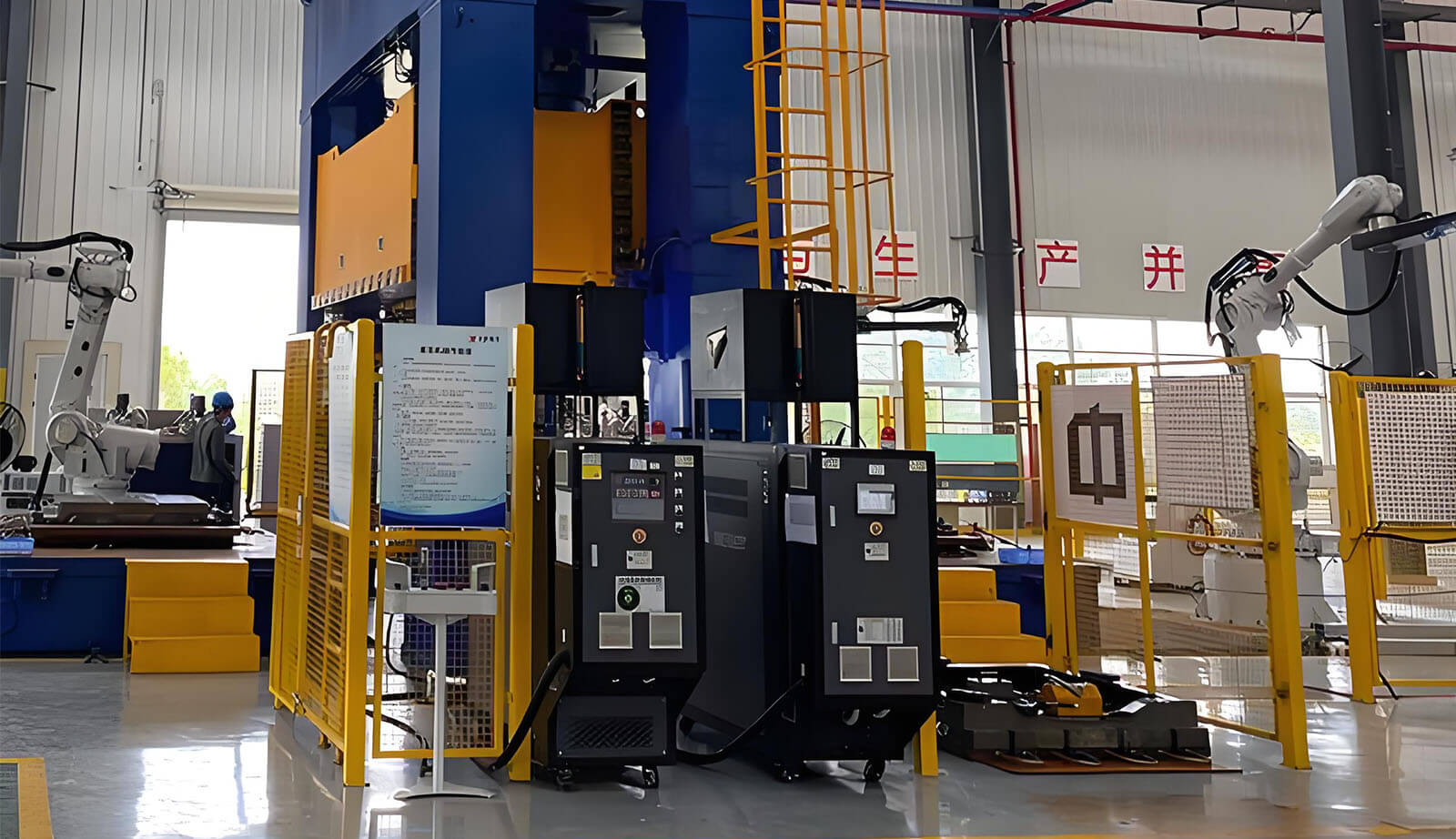
Carbon Fiber Composite Material Hot Pressing Molding Process
Our factory employs an advanced carbon fiber hot press process with a P20 steel mold, ensuring high efficiency, precision, durability, and cost-effectiveness for quality production.
Welcome to the world of forged carbon fiber! Our starter kit helps you make amazing parts for cars, planes, sports gear, and more. We are a top custom carbon fiber product manufacturing plant with years of making the best carbon parts.
Why pick our kit?
Forged carbon fibre is a new way to make carbon parts. It uses chopped carbon mixed with resin to make strong, good-looking parts. Unlike old weave carbon fiber, forged carbon has a cool marble look that many people love.
The forged carbon fibre process starts with chopped carbon fibers that get mixed with epoxy resin. Then we use heat and pressure to make the final part. This makes parts that are very strong but also look great. Our customers in aerospace, automotive, and sports equipment love how forged carbon parts are both light and strong. The random pattern of chopped fibers together gives each piece a one-of-a-kind look that stands out.
Our starter kit has everything you need to begin making forged carbon fibre components. Each kit includes:
Item | Quantity | Purpose |
---|---|---|
Chopped Carbon Tow | 500g | Main fiber material |
Premium Epoxy Resin | 1L | Binding agent |
Hardener | 500ml | Activates resin |
Release Wax | 100g | For easy part removal |
Compression Mold (sample) | 1 | For shaping parts |
Instruction Manual | 1 | Step-by-step guide |
Safety Gloves | 2 pairs | Protection |
Mixing Containers | 5 | For resin preparation |
The forged carbon fibre development kit is made for both new users and pros. Our epoxy resin system is the same one we use in our factory for high-performance parts.
“This kit changed how we make prototype parts. The quality is amazing and the support team helped us every step.” – John M., Automotive Design Engineer
Making forged carbon fibre parts is easy with our kit. Here’s how:
Our real carbon fiber materials provide excellent mechanical performance for all kinds of projects:
Our carbon fiber products are used in many top industries:
The moulding process we use makes parts that look great and work well. When strands of carbon are pressed together with the right amount of resin, they make parts that are better than regular laminate carbon.
Feature | Forged Carbon | Traditional Weave | Unidirectional |
---|---|---|---|
Look | Marble pattern | Regular weave | Straight lines |
Strength | Very high | High | Highest in one direction |
Ease of use | Easiest | Medium | Hardest |
Waste | Very low | Medium | High |
Curves | Excellent | Limited | Limited |
Cost | Medium | High | Highest |
When you buy forged carbon fiber from us, you get materials that are easy to work with. Unlike unidirectional carbon or prepreg materials, our forged carbon is more forgiving for complex shapes.
Our CT12 chopped carbon fiber system can be placed into a mold of almost any shape. This makes it perfect for making complex parts that would be hard with regular weave carbon fiber.
Benefits of our forged carbon process:
We use the same forging techniques as luxury car makers but make them work for your projects. Our composite materials are tested to meet the highest standards.
Our carbon fiber parts have helped many businesses:
“We switched to forged carbon for our motorcycle parts and sales went up 30%. Customers love the unique look.” – Mike T., Custom Motorcycle Shop
“The aerospace parts we make with this system passed all our tests. The weight savings are amazing.” – Sarah L., Aerospace Supplier
Our sports equipment line got a huge boost when we added forged carbon fiber options.” – David K., Sports Equipment Manufacturer
When you work with our forged carbon fibre components, you join companies that value quality and innovation. Our XCR coating resin gives parts a finish that lasts for years.
Ready to start making amazing forged carbon fibre parts? Here’s how to order:
For bigger projects, we offer full custom carbon fiber product manufacturing. Our factory can make parts from small to very large using our advanced compression moulds and expert team.
Order options:
Don’t wait to make carbon parts that will amaze your customers. Our forged carbon fibre development kit is the first step to creating parts that stand out. Contact us today to join the carbon fiber revolution!
Summary: Our Premium Forged Carbon Fiber Starter Kit gives you everything needed to create stunning, professional-grade carbon parts. With marble-like appearance, superior strength, and our expert support, you’ll be making amazing custom components for automotive, aerospace, and more in no time.
Our factory employs an advanced carbon fiber hot press process with a P20 steel mold, ensuring high efficiency, precision, durability, and cost-effectiveness for quality production.
Our factory runs 100+ hot pressure autoclaves, using aluminum molds and vacuum induction to shape carbon fiber with precision. High heat and pressure enhance strength, stability, and flawless quality.
Our Carbon Fiber Research Center drives innovation in new energy, intelligence, and lightweight design, using advanced composites and Krauss Maffei Fiber Form to create cutting-edge, customer-focused solutions.
Here are the answers to the frequently asked questions from the experienced carbon fiber products factory
We produce a wide range of carbon fiber components, including automotive parts, motorcycle parts, aerospace components, marine accessories, sports equipment, and industrial applications.
We primarily use high-quality prepreg carbon fiber and large-tow carbon fiber reinforced high-performance composites to ensure strength, durability, and lightweight characteristics.
Yes, our products are coated with UV-protective finishes to ensure long-lasting durability and maintain their polished appearance.
Yes, our facilities and equipment are capable of producing large-size carbon fiber components while maintaining precision and quality.
What are the benefits of using carbon fiber products?
Carbon fiber offers exceptional strength-to-weight ratio, corrosion resistance, stiffness, thermal stability, and a sleek, modern appearance.
We cater to automotive, motorcycle, aerospace, marine, medical, sports, and industrial sectors with a focus on lightweight and high-performance carbon fiber components.
Yes, we provide custom carbon fiber solutions tailored to your specifications, including unique designs, sizes, and patterns.
We utilize advanced technologies such as autoclave molding, hot pressing, and vacuum bagging, ensuring precision, stability, and quality in every product. wonders with the Hello Elementor Theme, we’re trying to make sure that it works great with all the major themes as well.
We use aluminum and P20 steel molds, designed for durability and high accuracy, to create complex and precise carbon fiber components.
Our products undergo rigorous quality control checks, including dimensional accuracy, material integrity, and performance testing, to meet industry standards.